Lean Production: Basics of methodical process optimization
Lean production refers to an organized production system with the goal of maximizing production efficiency and minimizing waste (Muda).
Production companies use lean production in order to be competitive in globalized production competition. In lean production, the methods 5S, Kaizen, Just-in-Time (JIT), Total Minute Exchange of Dies (SMED), Value Productive Maintenance (TPM) and Value Stream Mapping (VSM) are used.
Whether the implementation of lean production in a company is successful is measured using the seven key figures lead time (delivery time), cycle time, throughput, utilization, error rate, value-added ratio and overall equipment effectiveness (OEE).
Employees are a key success factor in lean production. Their involvement in decisions and improvement processes, training to expand their skills and their ability to make improvements independently are necessary to successfully implement the three principles of the Lean concept – value, value stream and flow.
The Lean Manufacturing System describes the concrete, holistic application of these principles throughout the entire production process and promotes continuous improvement and the active participation of all those involved.
What is Lean Production?
Lean Production (also known as Lean Manufacturing) translates to "schlanke Produktion" in German and refers to an organized production system aimed at maximizing the efficiency of production processes while minimizing waste.
Lean Production was originally developed by Toyota in the 1950s and has since been widely adopted in many production facilities worldwide for the purpose of process optimization.
Lean Production is a part of Lean Management. While Lean Production focuses on increasing the efficiency of production processes, Lean Management aims to optimize the entire value chain and all business processes.
What are the goals of Lean Production?
Lean production aims to achieve greater production efficiency, higher material quality, greater production flexibility and greater employee involvement in continuous improvement processes, problem-solving and decision-making within the framework of lean principles by optimizing processes and minimizing waste.
The increased efficiency results in improved competitiveness and sustainable corporate success.
Here are four examples of how GREIF-VELOX systems and their components achieve the goals of lean production:
Maximum efficiency
The use of GREIF-VELOX's energy-efficient and waste-minimizing filling and packaging technologies not only protects the environment, but also reduces operating costs. The precise calibration of the filling systems ensures that product accuracy is maximized, which minimizes material loss and increases resource efficiency.
The precise dosing systems from GREIF-VELOX adapt flexibly to different material properties and filling requirements. This results in less material loss and increased efficiency. A number of GREIF-VELOX filling systems for liquids and solids can also be easily adapted to different substance types and packaging sizes. This enables fast changeovers and increases overall productivity.
One example of this is the residual emptying process of the GREIF-VELOX gross pneumatic packer BVP: thanks to the special bowl outlet and the wet cleaning function, fast and hygienic material changes are guaranteed. Thanks to an innovative air flushing system and a conveyor belt for the removal of material residues, up to 95% less residual material remains in the bowl after the filling process than is usual in the industry, which not only makes cleaning easier, but also saves material. These processes prevent cross-contamination between the substances and also significantly reduce the cleaning effort required for substance changes: The effort involved drops from several hours to less than an hour, which significantly reduces plant downtimes.
By integrating intelligent software and IoT technologies, the systems enable real-time monitoring and precise analysis of production data. This not only improves efficiency, but also increases the flexibility of the entire process: production processes can be continuously optimized and adjustments can be made quickly and based on data. Thanks to the systematic evaluation of operating data, users are able to react agilely to changes in the market or in production and adapt their processes dynamically.
Higher quality
Systems such as ValvoDetect for valve bag filling identify and sort out faulty bags from the production process at an early stage. This ensures a high level of material protection and packaging quality and prevents contamination and material loss. Automated control mechanisms such as weighing systems ensure that each filling process takes place within the specified tolerances. Other features such as metal detectors or the extremely reliable GREIF-VELOX ValvoSaveSeal ultrasonic sealing unit ensure that the end product is neither contaminated by external influences nor can it leak out of the bag.
Greater flexibility
Filling systems from GREIF-VELOX can be easily integrated into existing production lines or expanded into complete production systems, so-called Full-line systems,, with load securing and robot palletizing. Their modular design, automated adaptation to different container sizes and intelligent control technology enable quick changeovers and high throughput rates. This makes them particularly efficient in production and flexible and adaptable to different requirements when filling solids, ultra-light substances and liquids.
Greater employee and customer participation
GREIF-VELOX attaches great importance to customer centricity and develops solutions in close cooperation with customers and employees. The aim is to solve industry-wide challenges in a targeted manner in order to create the greatest possible added value and competitive advantage for customers.
One example of this customer-oriented innovation strategy is the GREIF-VELOX UltraRubberBellow sealing sleeve, which significantly reduces material consumption and increases the service life of the system by up to 2,500%. The VeloFlexAdapt was also developed in co-creation with customers: This system enables smaller FIBCs to be filled with the GREIF-VELOX VeloVac XL vacuum packer, thereby increasing flexibility in production.
Each of these developments helps to continuously improve systems and components, reduce waste and increase productivity - in line with GREIF-VELOX's lean production philosophy.
What does the Lean concept say?
The Lean concept forms the theoretical basis of methodical lead production to improve efficiency and quality in production through process optimization and the elimination of waste.
The Lean concept is made up of the three pillars of value, value stream and flow.
Value
Value includes everything that a customer considers valuable and is willing to pay for.
A company must understand value from the customer's perspective and aim to maximize this value in its products and services. Employees play a crucial role in identifying and increasing value, as they are often in direct contact with processes and customer requirements. They can thus provide valuable insights and suggestions for increasing value.
Value Stream
The value stream describes the totality of all steps and processes required to produce a product or provide a service.
Employees are able to identify waste in the processes and make suggestions for improvement. Their active participation in value stream analysis and continuous improvement initiatives is therefore essential for the success of the company.
Flow
Flow refers to the continuous movement of products and information through the value stream without interruptions or waiting times.
The processes in the company should be designed so that they run without delays. Bottlenecks and waiting times are thereby minimized. This requires good coordination and integration of all process steps and the support of all employees.
You help to ensure a smooth flow by identifying bottlenecks and proposing solutions to optimize the workflow. Your flexibility and problem-solving skills are crucial to maintaining a continuous flow.
What does a Lean Manufacturing System look like?
A Lean Manufacturing System (Lean Process) is a holistic approach to overall production optimization based on minimizing waste and maximizing added value.
A typical Lean Manufacturing System consists of these nine process steps:
Identification of value from the customer's perspective
It is necessary to determine what the customer considers valuable and which product features and services create value for the customer.
Value stream analysis
All steps in the production process must be identified and documented. This involves analyzing which steps create value and which do not. Waste in the form of overproduction, waiting times, unnecessary transport routes, superfluous movements, stocks, errors and overprocessing must be eliminated.
Create flow
The processes must be designed so that they run without interruptions and bottlenecks. With the help of 5S, workplace organization is to be improved through sorting, systematizing, cleaning, standardizing and self-discipline.
Another aspect is the organization of production areas in U-shaped cells to improve material flow and communication.
Introduce a pull system
By implementing a Kanban system, material flow can be implemented based on actual demand. Just-in-time production also ensures that materials and products are only produced when they are needed. Inventory levels are thus minimized.
Continuous improvement (Kaizen)
Improvements are to be identified and implemented by conducting regular workshops. In addition, the Plan-Do-Check-Act cycle ensures systematic problem solving and process improvement.
Quality management
Total Quality Management (TQM) is a comprehensive quality management system to ensure product quality. It is also important to implement error prevention techniques to reduce defects (Poka-Yoke). The use of statistical methods to monitor and control processes (SPC) is also required.
Employee participation and development
Employees play a central role in lean production. They must be continuously trained in lean principles and lean methods. They should also be encouraged to take on responsibility and actively participate in improvements. To achieve this, it is important to generally promote teamwork within the company and to enable a culture of open communication and collaboration.
Visual management
Production processes should be supported through the use of diagrams, Kanban boards, Andon systems and other visual aids. Transparency is a crucial element in the lean process. Information about the production status and key performance indicators should be available in real time.
Technology and automation
Digital technologies and automation should be used to improve efficiency and data availability (Industry 4.0). In addition, the implementation of preventive maintenance strategies to ensure machine availability is an important aspect of the lean process.
What methods are there in lean production?
Lean production includes six methods that pursue different approaches to achieving the goals of lean production.
5S is a systematic approach to workplace organization. This method creates a clean, well-organized and safe work environment. This allows employees to work more effectively.
Kaizen aims to increase efficiency, quality and productivity through permanent, small, continuous improvements.
By means of Just-in-Time (JIT) production, it is specified that materials and goods are only produced or delivered at the time they are needed or required. In this way, inventory levels are reduced.
A drastic reduction in the set-up times (changeover times) of machines and systems is achieved through the Single Minute Exchange of Dies (SMED).
The goal of Total Productive Maintenance (TPM) is to maximize the effectiveness and efficiency of production facilities through preventive and predictive maintenance measures.
With Value Stream Mapping (VSM), all steps of a production process are visually displayed, which allows inefficient processes to be identified and eliminated.
5S
5S is a systematic approach to workplace organization and improving efficiency by creating a clean, well-organized and safe working environment.
5S comprises five measures, each of which represents a process step:
- Seiri (sorting): Separation of the required of unused materials and tools. Everything unnecessary is removed.
- Seiton (systematize): Organize the remaining materials and tools so that they are easily accessible and in order.
- Seiso (clean): Clean the workplace and maintain it regularly to maintain cleanliness and order.
- Seiketsu (standardize): Develop and introduce standards for organizing and cleaning the workplace.
- Shitsuke (self-discipline): Ensuring compliance with standards and promoting a culture of continuous improvement.
5S has the advantage that it results in a clean and optimally organized workplace, which has many positive effects. Employees do not waste time looking for materials or tools. Good organization minimizes errors and improves product quality. The risk of accidents is significantly reduced by a well-organized workplace and the general satisfaction of employees increases.
Without consistent application, 5S does not work and so it also brings with it some potential disadvantages. The constant discipline required to comply with 5S can be perceived as extremely strenuous and challenging. Especially at the beginning, implementing the method can be time-consuming and costly, as all employees have to be trained and the work areas have to be reorganized. It is also important that the 5S method does not contain standards that are too strict or inflexible. This would limit the creativity and flexibility of employees.
Kaizen
Kaizen means "change for the better" and is a method of Japanese origin that aims to increase the efficiency, quality and productivity of processes through small, continuous improvements. All employees of a company, regardless of their hierarchical level, are actively involved in improvement processes.
Kaizen has the advantage that the constant identification and elimination of waste not only optimizes workflows and makes better use of resources, but also reduces costs and increases efficiency.
Kaizen creates an environment in which companies react quickly to market changes and new requirements through regular small changes. At the same time, innovation is promoted because employees are encouraged to find creative solutions to existing problems. This results in increased employee satisfaction.
Kaizen's disadvantage is primarily due to the time it takes. The results of Kaizen often only become apparent in the long term, which is seen as a disadvantage in fast-moving business environments. The implementation of Kaizen also requires a significant initial investment of time and resources, especially for training and establishing a Kaizen culture. Kaizen requires continuous monitoring and adaptation. This also leads to a strain on resources in the long term.
Just in Time (JIT)
Just-in-Time (JIT) is a production and delivery concept that is designed to deliver materials and goods exactly when they are needed in order to minimize inventory levels.
Since this method only orders and delivers materials and products when they are needed, the advantages are clear: On the one hand, the costs of warehousing and the risks of excess inventory are reduced, and on the other hand, the efficiency of the entire production process is increased by the precise coordination of delivery times and production processes.
Companies can react quickly to changes in demand and adjust production plans accordingly, which enables greater flexibility in the production process.
Just-in-Time, however, has the disadvantage that it requires a lot of planning and coordination. Close cooperation and reliability of suppliers are essential. The method is therefore very risky. Any delay or disruption in the supply chain can affect the entire production.
Total Minute Exchange of Dies (SMED)
Single Minute Exchange of Dies (SMED) aims to drastically reduce the set-up times (changeover times) of machines and systems. The change of tools and fixtures should be optimized so that it can be carried out in less than ten minutes (i.e. in single-digit minutes, "single minute").
By reducing set-up times, machines and systems change more quickly from one production run to the next, which has the clear advantage of increasing machine availability and production efficiency. This allows companies to respond more flexibly to changes in demand, which leads to better adaptation to customer requirements. In addition, inventories of intermediate and final products are reduced, thus reducing storage costs.
But there are also disadvantages. Single Minute Exchange of Dies (SMED) incurs significant initial implementation costs. Training, process analysis and possibly new equipment are required. In addition, not all machines and processes are equally suitable for SMED.
Value Productive Maintenance (TPM)
The goal of Total Productive Maintenance (TPM) is to maximize the effectiveness and efficiency of production facilities through preventive and predictive maintenance measures. TPM aims to fully involve all employees in the maintenance processes.
The method has several advantages, including that preventive maintenance minimizes downtime while maximizing production output. This also means that the service life of the facilities is extended. The maintained machines function optimally, the quality of the goods produced increases and the risk of machine errors and accidents is reduced.
The disadvantage is that Total Productive Maintenance requires a lot of effort in coordinating and planning preventive maintenance measures. To maintain the efficiency of TPM, continuous training and education of employees is required, which is costly and time-consuming.
Value Stream Mapping (VSM)
Value Stream Mapping (VSM) is used to visually represent all steps of a production process. The aim of this method is to analyze and optimize the flow of materials and information from the order placement to delivery to the customer.
Advantages are clear: The clear and comprehensive visualization of the entire production process enables both value-adding and non-value-adding activities (waste) to be identified within the process. This gives the company the optimal basis for improvement measures. This method also promotes better communication and collaboration between different departments and teams, as everyone involved develops a common understanding of the entire process and the existing problems.
A disadvantage of Value Stream Mapping is that the method can lead to a static view of processes that does not adequately reflect dynamic and rapidly changing environments.
How can lean production be developed in a company
The development of lean production in a company requires a systematic and structured approach that includes several phases and initiatives.
These are the essential steps for implementing lean production in a company:
Understanding
In the first step of developing lean production, company management must support and actively promote lean principles. At the same time, it is important that employees develop an understanding of how to implement lean production. At this point, it is recommended to bring in a consultant or lean expert to support the process and gain an understanding of lean production with the help of best practice examples.
Analysis
The second step is a detailed analysis of the current situation. For this purpose, all steps in the production process should be identified and documented. Detailed process flow diagrams help to optimally visualize the current production process. Regular visits to the production facilities by management (Gemba Walks) serve to identify opportunities for improvement directly on site. In this context, waste in the production process should also be identified.
The seven types of waste (Muda) are:
- Overproduction
- Waiting times
- Transport
- Overprocessing
- Inventories
- Movements
- Defects
Improvement plan
In the third step, concrete improvement measures are to be developed together with the employees using Kaizen workshops. The PDCA cycle (Plan-Do-Check-Act) helps with problem solving and process improvement through systematic planning, implementation, checking and action. At this point, it is important to develop and establish standard operating procedures (SOPs) to ensure consistent workflows.
Implementation
In the fourth step, the lean methods described above are implemented. 5S, Just-in-Time (JIT), Kaizen, Single Minute Exchange of Dies (SMED), Total Productive Maintenance (TPM), Value Stream Mapping (VSM).
Monitoring
In order to measure and ensure the success of lean production in a company, progress must be monitored in the fifth step. To do this, it is crucial to define key performance indicators (KPIs) that can be used to measure progress and identify opportunities for improvement. Regular audits should be carried out to check compliance with the lean principles and evaluate the progress achieved.
Long-term
Finally, a long-term strategy for continuous improvement and adaptation of the lean principles to changing conditions in the company must be developed. Through the interaction of these systematic steps, lean production is successfully implemented in a company.
What are the central production factors of lean production?
The seven production factors of lean production are:
- Human resources
- Materials
- Machines and technologies
- Methods and processes
- Information
- Workplace design
- Customer satisfaction
The production factors of lean production are closely linked and must be optimized in harmony in order to fully exploit the benefits of lean production.
Human resources
Lean production places great value on teamwork, training, continuous improvement (Kaizen) and proactive collaboration by employees. Every employee should be motivated to contribute their own ideas and opinions. In addition, managers play a crucial role in a functioning lean culture. Lean production can only be successful in the company through their support and role model function.
Materials
A central production factor in lean production is materials, goods and means of production. Their stocks should be reduced to a minimum so that storage costs are reduced and flexibility is increased. All goods produced should be of high quality in order to minimize errors and rework.
Machines and technologies
Lean production requires the use of modern and efficient machines that are easy to maintain and can be used flexibly.
Methods and processes
Minimizing waste and continuously optimizing production processes are the core of lean production. The value streams in the company must be analyzed in order to identify and eliminate waste. Standardized work instructions (SOPs) help to ensure consistent and efficient processes. Basically, a culture of continuous improvement should be established in which all employees are constantly looking for opportunities for improvement.
Information
Lean production requires visual management to support production processes and improve transparency. Diagrams, Kanban boards and Andon systems are ideal for this. In addition, information in the form of performance data and key performance indicators (KPIs) is collected and analyzed to measure progress and make decisions.
Workplace design
5S in particular serves to optimize work organization and workplace cleanliness. The workplace must also be designed from an ergonomic perspective in order to maintain the health and working ability of employees.
Customer satisfaction
Lean production promotes the alignment of production with the requirements and expectations of customers. The company must be able to respond quickly to changes in customer demand and market conditions. The goal is to increase customer satisfaction, also in order to avoid resource-consuming complaints.
What key figures are used to measure the success of lean production
To measure the success of Lean Production, various indicators are used that provide information about the efficiency and effectiveness of the production processes.
The seven most important success indicators of Lean Production are:
Lead Time (delivery time)
The time span from placing an order to the delivery of a finished product is called lead time.
GREIF-VELOX systems optimize and automate filling and packaging processes. Both reduce lead time significantly.
Cycle time
Cycle time is the time it takes for a product to go through a specific production process from start to finish.
GREIF-VELOX systems reduce cycle time by working faster and eliminating bottlenecks in the packaging and handling processes.
Throughput
The amount of products produced in a certain period of time is called throughput.
The high efficiency and automation of GREIF-VELOX systems means that more products are filled, bagged or packaged and made available in less time. This increases throughput.
Utilization
Utilization refers to the percentage of available production capacity that is actually used.
GREIF-VELOX systems work continuously and efficiently. This means that production capacity is used optimally.
Error rate
The error rate is the percentage of units produced that are defective.
Using GREIF-VELOX systems significantly reduces the error rate in companies. The systems work precisely and reliably, thus minimizing errors in the packaging processes.
Value-added ratio
The value-added ratio is the proportion of value-added time to the total production time.
The automation and efficiency of GREIF-VELOX systems increases the value-added ratio because more time is spent on value-added activities and less time on non-value-added activities.
Overall Equipment Effectiveness (OEE)
The key figure for measuring the productivity of a system, which is made up of availability, performance and quality, is called Overall Equipment Effectiveness (OEE).
GREIF-VELOX systems improve OEE by ensuring high availability (less downtime), high performance (fast and efficient processing) and high quality (low error rate).
What significance does lean production have for companies in globalized production competition?
Companies implement lean production in order to remain competitive in global production competition, reduce costs, increase efficiency and respond flexibly to constantly changing market conditions.
Filling systems and packaging systems from GREIF-VELOX help companies to introduce and implement lean production in their production operations. In particular, the parameters of production speed, measurement or filling accuracy and production reliability are improved by GREIF-VELOX systems.
Example: Lean production in the chemical industry
In the chemical industry, maximum precision, safety and cleanliness are the main requirements for all production-related filling processes. The lean method "Just in Time" supports precise work by synchronizing material availability precisely with production requirements. In this way, a company can reduce its inventory and increase flexibility.
Kaizen ensures continuous improvement of processes. This results in a lower error rate and higher manufacturing precision. In addition, the Poka Yoke lean method promotes production precision by using error prevention techniques to ensure that production processes are automatically optimized before errors occur.
The safety aspect is particularly important in the chemical industry. Lean production promotes standardized processes and continuous improvements, thereby ensuring greater safety. Lean methods minimize malfunctions and accidents through strict process controls and preventive maintenance. These measures increase employee safety.
Chemical and food industry
Innovative solids filling system for ICL Ladenburg
The solid filling system from GREIF-VELOX at ICL Ladenburg led to a significant reduction in complaint and cleaning costs, which were originally caused by incorrectly welded bags. This cost problem, which amounted to at least 20,000 euros annually, was radically improved by the introduction of the ValvoDetect on the BVP air packer. With its optical sensors, ValvoDetect ensures that only correctly positioned bags are welded by detecting and sorting out incorrectly attached bags before welding.
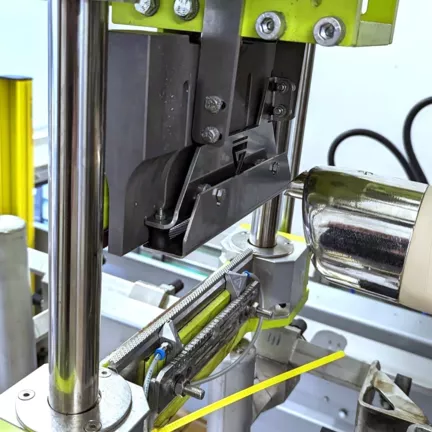
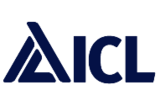
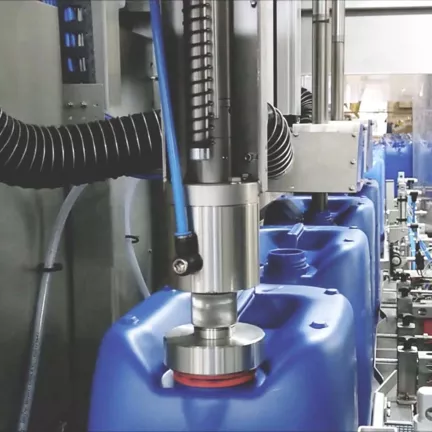
Chemical industry
Hydrogen peroxide filling system for Evonik
Our filling system at the chemical company Evonik led to an impressive increase in filling speed by 50 percent. Additionally, we significantly improved product safety by implementing advanced contamination control measures integrated into a highly automated hydrogen peroxide filling system, increasing not only efficiency but also workplace safety.
Regular cleaning improves cleanliness and order, which are of great importance in companies in the chemical industry. Lean Production supports the introduction and strict adherence to standardized cleaning procedures through the application of the 5S method.
Through continuous improvement processes (Kaizen), potential weak points in terms of cleanliness are constantly identified and remedied. The use of visual management can clearly communicate and check cleanliness standards. Color-coded areas, checklists and visual instructions help to ensure compliance with cleaning standards. Visible checkpoints and regular inspections make it easier to monitor and ensure the cleanliness status in real time.
The use of Poka Yoke (error prevention) ensures that systems are cleaned automatically to avoid human error. Lean Production emphasizes the importance of documenting all cleaning processes. Complete documentation helps to prove compliance with cleanliness standards and to be ready for inspections or audits.
Example: Lean production in the food industry
Filling solutions for the food industry must be hygienic, precise and reliable. This is the only way to reliably meet the specific requirements of this industry. Hygienic filling processes prevent food from being contaminated with harmful bacteria, viruses, parasites and chemicals that cause food poisoning and serious health problems.
In addition, hygiene during filling ensures compliance with legal requirements. Lean production promotes the introduction and adherence to standardized cleaning procedures so that the hygiene of all filling systems is ensured.
The 5S method in the food industry ensures that
- unnecessary materials and tools are removed from the work area to prevent the accumulation of dirt,
- workstations are organized to ensure that cleaning equipment and agents are easily accessible and ready for use,
- hygiene is ensured through regular and systematic cleaning of work areas and machines,
- standards for cleanliness and order are introduced and
- cleanliness standards are sustainably maintained through regular inspections and training.
Through continuous improvement processes (Kaizen), potential hygiene risks are identified and remedied in lean production. The use of visual management also serves to clearly communicate and check hygiene standards. Thanks to the automatic monitoring systems (Poka Yoke), contamination is detected and displayed.
Food industry
Bagging system for GoodMills Germany
At the food producer GoodMills Germany, we were able to significantly increase packaging efficiency by 100 percent thanks to our systems. We also maximized the accuracy of the filling processes, doubling production output to up to 400 bags per hour, while at the same time minimizing cleaning effort and changeover times by using our gross pneumatic packer BVPV 4.40.
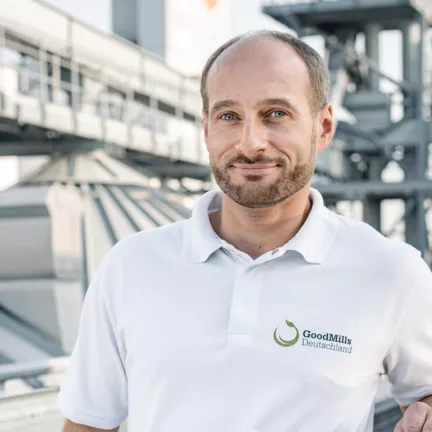
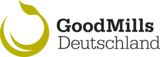
Example: Lean Production in Petrochemicals
In the petrochemical industry, many products are toxic, flammable, otherwise hazardous and often have complex chemical properties that require special materials and equipment and manufacturing designs.
The filling solutions must therefore be robust, high-performance and adaptable to meet the specific needs of this industry. Lean Production supports the high requirements and challenges for robust and high-performance filling and packaging systems in the petrochemical industry through "Total Productive Maintenance" strategies.
These strategies ensure that the filling systems remain high-performance by regularly maintaining them. The involvement of machine operators in the maintenance processes increases the reliability of the systems because problems are identified and resolved at an early stage.
In addition, Kaizen promotes the continuous search for opportunities for improvement in the filling processes, which enables high-performance operations. Lean Production avoids unnecessary inventory by synchronizing production and demand. This increases the performance of the filling processes. Visual management creates the necessary transparency in the production process to make it easier to identify and resolve problems and thus ensure consistent performance.
The adaptability of filling plants and packaging systems required in the petrochemical industry promotes lean production through the implementation of just-in-time principles. Companies can quickly adapt their production to changing demand conditions by providing materials and products at exactly the right time.
Lean production ensures that SMED techniques significantly reduce set-up times, allowing the filling process to quickly switch between different products. By standardizing changeover processes, set-up operations can be carried out efficiently and consistently, which increases adaptability. The use of scalable technologies that can be easily adapted to different production volumes without having to make significant changes to the infrastructure increases adaptability enormously.
Where can lean concepts and lean measures be used outside of production?
Lean production focuses primarily on optimizing production processes by minimizing waste and maximizing efficiency. These principles have proven to be extremely successful in the area of manufacturing and have led to significant improvements, particularly in productivity and quality, as the above examples from the chemical and food industries have shown.
However, the application of lean principles is not limited to manufacturing or production. In order to achieve the full effect of lean, these principles must be extended to the entire organization. This is where lean management comes in. Lean management applies the concepts of lean production to all business areas and processes within a company.
What is lean management?
So while Lean Production targets manufacturing, Lean Management aims to create a comprehensive culture of continuous improvement and efficiency throughout the company. It is about eliminating waste in all forms, be it in administration, customer service or other support functions.
By implementing Lean Management, companies can create a holistic, lean and efficient organization that is better able to adapt to change and be sustainably competitive.
Lean Management is based on the same principles of the Lean concept and therefore requires the same process steps: identifying value from the customer's perspective, identifying the value stream, creating flow, introducing a pull system and striving for perfection, which includes quality management, employee participation and development, visual management and technology and automation.