Lean Production: Grundlagen methodischer Prozessoptimierung
Lean Production bezeichnet ein organisiertes Produktionssystem mit dem Ziel, die Produktionseffizienz zu maximieren und Verschwendung (Muda) zu minimieren.
Produktionsbetriebe setzen Lean Production ein, um im globalisierten Produktionswettbewerb konkurrenzfähig zu sein. In der Lean Production kommen dafür die Methoden 5S, Kaizen, Just-in-Time (JIT), Total Minute Exchange of Dies (SMED), Value Productive Maintenance (TPM) und Value Stream Mapping (VSM) zum Einsatz.
Ob die Implementierung einer Lean Production in einem Unternehmen erfolgreich verläuft, wird anhand der sieben Kennzahlen Lead Time (Lieferzeit), Durchlaufzeit, Durchsatz (Throughput), Auslastung (Utilization), Fehlerrate (Error Rate), Wertschöpfungsgrad (Value-Added Ratio) und Overall Equipment Effectiveness (OEE) gemessen.
Mitarbeiter sind ein wesentlicher Erfolgsfaktor in der Lean Production. Ihre Einbindung in Entscheidungen und Verbesserungsprozesse, Schulungen, um ihre Fähigkeiten zu erweitern, und ihre Befähigung, eigenständig Verbesserungen vorzunehmen, sind notwendig, um die drei Prinzipien des Lean-Konzepts – Wert, Wertstrom und Fluss – erfolgreich umzusetzen.
Das Lean Manufacturing System bezeichnet die konkrete, ganzheitliche Anwendung dieser Prinzipien im gesamten Produktionsprozess und fördert kontinuierliche Verbesserungen und die aktive Mitarbeit aller Beteiligten.
Was ist Lean Production?
Lean Production (auch Lean Manufacturing) heißt ins Deutsche übersetzt „schlanke Produktion“ und bezeichnet ein organisiertes Produktionssystem, das darauf abzielt, die Effizienz von Produktionsprozessen zu maximieren und Verschwendung zu minimieren.
Lean Production wurde ursprünglich von Toyota in den 1950er Jahren entwickelt und hat sich seitdem weltweit in vielen Produktionsbetrieben mit dem Zweck der Prozessoptimierung etabliert.
Lean Production ist ein Bestandteil des Lean Managements. Während Lean Production sich auf die Effizienzsteigerung von Produktionsprozessen konzentriert, strebt Lean Management eine Optimierung der gesamten Wertschöpfungskette und aller Unternehmensprozesse an.
Welche Ziele verfolgt Lean Production?
Lean Production verfolgt das Ziel, durch Prozessoptimierung und Verschwendungsminimierung eine höhere Produktionseffizienz, höhere Stoffqualität, höhere Produktionsflexibilität und eine stärkere Beteiligung der Mitarbeiter an kontinuierlichen Verbesserungsprozessen, Problemlösungen und Entscheidungsfindungen im Rahmen der Lean-Prinzipien zu erreichen.
Aus der gesteigerten Effizienz resultieren eine verbesserte Wettbewerbsfähigkeit und nachhaltiger Unternehmenserfolg.
Folgend vier Beispiele, wie GREIF-VELOX-Anlagen und ihre Komponenten die Ziele von Lean Production erreichen:
Maximale Effizienz
Der Einsatz der energieeffizienten und abfallminimierenden Abfüll- und Verpackungstechnologien von GREIF-VELOX schont nicht nur die Umwelt, sondern senkt auch Betriebskosten. So sorgt die genaue Kalibrierung der Abfüllanlagen für eine Maximierung der Produktgenauigkeit, was den Stoffverlust minimiert und die Ressourceneffizienz erhöht.
Die präzisen Dosiersysteme von GREIF-VELOX passen sich flexibel an verschiedene Stoffeigenschaften und Abfüllanforderungen an. Dies führt zu einem geringeren Stoffverlust und einer gesteigerten Effizienz. Eine Anzahl von Abfüllanlagen von GREIF-VELOX sind in den Bereichen Flüssigkeiten und Feststoffe außerdem jeweils leicht an unterschiedliche Stofftypen und Verpackungsgrößen anpassbar. So sind schnelle Stoffwechsel möglich und die Gesamtproduktivität erhöht sich.
Ein Beispiel dafür ist das Restentleerungsverfahren des GREIF-VELOX Bruttopneumatikpacker BVP: Dank speziellem Kesselauslauf sowie der Nassreinigungsfunktion werden schnelle und hygienische Stoffwechsel gewährleistet. Durch ein innovatives Luftspülsystem und ein Förderband für den Abtransport von Stoffresten verbleiben nach dem Abfüllprozess bis zu 95 Prozent weniger Reststoffmenge im Kessel als branchenüblich, was nicht nur die Reinigung erleichtert, sondern auch Stoff einspart. Durch diese Verfahren werden sowohl Kreuzkontaminationen zwischen den Stoffen verhindert als auch der Reinigungsaufwand bei Stoffwechseln erheblich reduziert: Der Aufwand sinkt von mehreren Stunden auf weniger als eine Stunde, was die Stillstandzeiten der Anlage erheblich verkürzt.
Durch die Integration intelligenter Software und IoT-Technologien ermöglichen die Anlagen eine Echtzeitüberwachung sowie eine präzise Analyse der Produktionsdaten. Dies verbessert nicht nur die Effizienz, sondern steigert auch die Flexibilität des gesamten Prozesses: Produktionsabläufe lassen sich kontinuierlich optimieren, Anpassungen können schnell und datenbasiert erfolgen. Dank der systematischen Auswertung der Betriebsdaten sind Anwender in der Lage, agil auf Veränderungen im Markt oder in der Produktion zu reagieren und ihre Prozesse dynamisch anzupassen.
Höhere Qualität
Systeme wie ValvoDetect zur Ventilsack-Abfüllung identifizieren und sortieren fehlerhafte Säcke frühzeitig aus dem Produktionsprozess aus. Hoher Stoffschutz sowie hohe Verpackungsqualität sind somit sichergestellt und Kontamination sowie Stoffverlust sind ausgeschlossen. Automatisierte Kontrollmechanismen wie Wägesysteme stellen sicher, dass jeder Abfüllprozess innerhalb der festgelegten Toleranzen erfolgt. Weitere Features wie Metall-Detektoren oder die äußerst zuverlässige Ultraschallverschweißeinheit GREIF-VELOX ValvoSaveSeal sorgen dafür, dass das Endprodukt weder durch äußere Einflüsse verunreinigt wird noch aus dem Sack austreten kann.
Höhere Flexibilität
Abfüllanlagen von GREIF-VELOX lassen sich leicht in bestehende Produktionslinien integrieren oder zu vollständigen Produktionssystemen, sogenannten Full-Line-Anlagen, mit Ladungssicherung und Roboterpalettierung ausbauen. Ihre modulare Bauweise, die automatisierte Anpassung an unterschiedliche Gebindegrößen sowie die intelligente Steuerungstechnologie ermöglichen eine schnelle Umrüstung und hohe Durchsatzraten. Dadurch sind sie besonders effizient in der Produktion und flexibel und bei der Abfüllung von Feststoffen, ultraleichten Stoffen und Flüssigkeiten jeweils an verschiedene Anforderungen anpassbar.
Stärkere Mitarbeiter- und Kundenbeteiligung
GREIF-VELOX legt großen Wert auf Kundenzentrierung und entwickelt Lösungen in enger Zusammenarbeit mit Kunden und Mitarbeitenden. Ziel ist es, branchenweit bestehende Herausforderungen gezielt zu lösen, um einen möglichst hohen Mehrwert und Wettbewerbsvorteil für die Kunden zu schaffen.
Ein Beispiel für diese kundenorientierte Innovationsstrategie ist die Dichtmanschette GREIF-VELOX UltraRubberBellow, die den Materialverbrauch erheblich reduziert und die Standzeit der Anlage um bis zu 2.500 % erhöht. Ebenso entstand der VeloFlexAdapt in Co-Creation mit Kunden: Dieses System ermöglicht, mit dem Vakuumpacker GREIF-VELOX VeloVac XL auch kleinere FIBCs zu befüllen und so die Flexibilität in der Produktion zu erhöhen.
Jede dieser Entwicklungen trägt dazu bei, Anlagen und Komponenten kontinuierlich zu verbessern, Verschwendung zu reduzieren und die Produktivität zu steigern – ganz im Sinne der Lean Production Philosophie von GREIF-VELOX.
Was besagt das Lean-Konzept?
Das Lean-Konzept bildet die theoretische Grundlage der methodischen Lead Production zur Verbesserung der Effizienz und Qualität in der Produktion durch Prozessoptimierung sowie die Beseitigung von Verschwendung.
Das Lean-Konzept setzt sich aus den drei Säulen Wert, Wertstrom und Fluss zusammen.
Wert (Value)
Wert umfasst alles, das ein Kunde als wertvoll ansieht und wofür er bereit zu zahlen ist.
Ein Unternehmen muss den Wert aus der Sicht des Kunden verstehen und darauf abzielen, diesen Wert in seinen Produkten und Dienstleistungen zu maximieren. Die Mitarbeitenden spielen eine entscheidende Rolle bei der Identifizierung und Steigerung des Wertes, da sie oft in direktem Kontakt mit den Prozessen und Kundenanforderungen stehen. Sie können so wertvolle Einblicke und Vorschläge zur Wertsteigerung liefern.
Wertstrom (Value Stream)
Der Wertstrom beschreibt die Gesamtheit aller Schritte und Prozesse, die zur Herstellung eines Produkts oder zur Erbringung einer Dienstleistung erforderlich sind.
Die Mitarbeitenden sind in der Lage, Verschwendung in den Prozessen zu erkennen und Vorschläge zur Verbesserung zu machen. Ihre aktive Beteiligung an der Wertstromanalyse und an kontinuierlichen Verbesserungsinitiativen ist daher für den Erfolg des Unternehmens unerlässlich.
Fluss (Flow)
Fluss bezeichnet die kontinuierliche Bewegung von Produkten und Informationen durch den Wertstrom ohne Unterbrechungen und Wartezeiten.
Die Prozesse sollen im Unternehmen so gestaltet werden, dass sie ohne Verzögerungen ablaufen. Engpässe und Wartezeiten werden dadurch minimiert. Dies erfordert eine gute Abstimmung und Integration aller Prozessschritte sowie die Unterstützung aller Mitarbeitenden.
Sie tragen dazu bei, einen reibungslosen Fluss zu gewährleisten, indem sie Engpässe identifizieren und Lösungen zur Optimierung des Arbeitsflusses vorschlagen. Ihre Flexibilität und Fähigkeit zur Problemlösung sind entscheidend für die Aufrechterhaltung eines kontinuierlichen Flusses.
Wie sieht ein Lean Manufacturing System aus?
Ein Lean Manufacturing System (Lean-Prozess) ist ein ganzheitlicher Ansatz zur gesamten Produktionsoptimierung, der auf der Minimierung von Verschwendung und der Maximierung der Wertschöpfung basiert.
Ein typisches Lean Manufacturing System setzt sich zusammen aus diesen neun Prozessschritten:
Identifikation von Wert aus Kundensicht
Es ist zu bestimmen, was der Kunde als wertvoll erachtet und welche Produkteigenschaften und Dienstleistungen einen Wert für den Kunden schaffen.
Wertstromanalyse
Alle Schritte im Produktionsprozess sind zu identifizieren und zu dokumentieren. Hierbei gilt es zu analysieren, welche Schritte wertschöpfend sind und welche nicht. Verschwendung in Form von Überproduktion, Wartezeiten, unnötigen Transportwegen, überflüssigen Bewegungen, Beständen, Fehlern und Überbearbeitung müssen eliminiert werden.
Fluss schaffen (Flow)
Die Prozesse sind so zu gestalten, dass sie ohne Unterbrechung und Engpässe ablaufen. Mit Hilfe von 5S soll die Arbeitsplatzorganisation durch Sortieren, Systematisieren, Säubern, Standardisieren und Selbstdisziplin verbessert werden.
Ein weiterer Aspekt ist die Organisation der Produktionsbereiche in U-förmigen Zellen, um den Materialfluss und die Kommunikation zu verbessern.
Pull-System einführen
Durch die Implementierung eines Kanban-Systems kann der Materialfluss basierend auf der der tatsächlichen Nachfrage implementiert werden. Just-in-Time-Produktion sorgt zusätzlich dafür, dass Materialien und Produkte nur dann hergestellt werden, wenn sie benötigt werden. Lagerbestände werden damit minimiert.
Kontinuierliche Verbesserung (Kaizen)
Durch die Durchführung regelmäßiger Workshops sollen Verbesserungen identifiziert und umgesetzt werden. Zusätzlich sorgt der Plan-Do-Check-Act-Zyklus für systematische Problemlösung und Prozessverbesserung.
Qualitätsmanagement
Das Total Quality Management (TQM) stellt ein umfassendes Qualitätsmanagement zur Sicherstellung der Produktqualität dar. Es gilt darüber hinaus, Fehlervermeidungstechniken zur Reduzierung von Defekten zu implementieren (Poka-Yoke). Auch der Einsatz statistischer Methoden zur Überwachung und Steuerung von Prozessen (SPC) ist gefordert.
Mitarbeiterbeteiligung und –entwicklung
Die Mitarbeiter spielen eine zentrale Rolle in der Lean Production. Sie müssen kontinuierlich in Lean-Prinzipien und Lean-Methoden geschult werden. Außerdem sollen sie ermutigt werden, Verantwortung zu übernehmen und aktiv an Verbesserungen mitzuwirken. Dafür ist es wichtig, die Teamarbeit im Unternehmen generell zu fördern und eine Kultur der offenen Kommunikation und Zusammenarbeit zu ermöglichen.
Visuelles Management
Durch den Einsatz von Schaubildern, Kanban-Boards, Andon-Systemen und anderen visuellen Hilfsmitteln sollen die Produktionsprozesse unterstützt werden. Die Transparenz ist im Lean-Prozess ein entscheidendes Element. Informationen über den Produktionsstatus und Leistungskennzahlen sollen in Echtzeit bereitstehen.
Technologie und Automatisierung
Digitale Technologien und Automatisierung sollen zur Verbesserung der Effizienz und Datenverfügbarkeit genutzt werden (Industrie 4.0). Außerdem ist die Implementierung von vorbeugenden Wartungsstrategien zur Sicherstellung der Maschinenverfügbarkeit ein wichtiger Aspekt im Lean-Prozess.
Welche Methoden gibt es in der Lean Production?
Lean Production umfasst sechs Methoden, die unterschiedliche Ansätze verfolgen, um die Ziele der Lean Production zu erreichen.
5S ist ein systematischer Ansatz zur Arbeitsplatzorganisation. Mit dieser Methode wird die Schaffung einer sauberen, gut organisierten und sicheren Arbeitsumgebung erreicht. Dadurch arbeiten Mitarbeiter effektiver.
Kaizen zielt darauf ab, durch permanente kleine, kontinuierliche Verbesserungen eine Steigerung der Effizienz, Qualität und Produktivität zu erreichen.
Mittels einer Fertigung Just-in-Time (JIT) ist vorgegeben, dass Materialien und Waren ausschließlich zum benötigten oder geforderten Zeitpunkt produziert bzw. geliefert werden. Auf diese Weise werden Lagerbestände reduziert.
Ein drastisches Reduzieren der Rüstzeiten (Umrüstzeiten) von Maschinen und Anlagen wird durch die Single Minute Exchange of Dies (SMED) erreicht.
Das Ziel von Total Productive Maintenance (TPM) ist, die Effektivität und Effizienz von Produktionsanlagen durch präventive und vorausschauende Wartungsmaßnahmen zu maximieren.
Mit Value Stream Mapping (VSM) werden alle Schritte eines Produktionsprozesses visuell dargestellt, wodurch sich ineffiziente Abläufe identifizieren und beheben lassen.
5S
5S ist ein systematischer Ansatz zur Arbeitsplatzorganisation und zur Verbesserung der Effizienz durch die Schaffung einer sauberen, gut organisierten und sicheren Arbeitsumgebung.
5S umfasst fünf Maßnahmen, die jeweils einen Prozessschritt abbilden:
- Seiri (Sortieren): Trennung der benötigten von nicht benötigten Materialien und Werkzeugen. Alles Unnötige wird entfernt.
- Seiton (Systematisieren): Organisation der verbleibenden Materialien und Werkzeuge, sodass sie leicht zugänglich und geordnet sind.
- Seiso (Säubern): Reinigung des Arbeitsplatzes und regelmäßige Pflege, um Sauberkeit und Ordnung zu erhalten.
- Seiketsu (Standardisieren): Entwicklung und Einführung von Standards für die Organisation und Reinigung des Arbeitsplatzes.
- Shitsuke (Selbstdisziplin): Sicherstellung der Einhaltung von Standards und Förderung einer kontinuierlichen Verbesserungskultur.
5S hat den Vorteil, dass aus ihr ein sauberer und optimal aufgeräumter Arbeitsplatz resultiert, der viele positive Effekte mitbringt. So verschwenden die Mitarbeiter keine Zeit mit dem Suchen von Materialien oder Werkzeugen. Durch die gute Organisation werden Fehler minimiert und die Produktqualität verbessert sich. Das Risiko von Unfällen wird durch einen gut organisierten Arbeitsplatz erheblich gemindert und die allgemeine Zufriedenheit der Mitarbeiter steigt.
Ohne eine konsequente Anwendung funktioniert 5S nicht, und so bringt sie auch einige potenzielle Nachteile mit sich. Die ständig erforderliche Disziplin zu Einhaltung von 5S kann als äußerst anstrengend und herausfordernd wahrgenommen werden. Vor allem zu Beginn kann die Implementierung der Methode zeit- und kostenintensiv sein, da alle Mitarbeiter geschult und die Arbeitsbereiche neu organisiert werden müssen. Es ist vor allem auch wichtig, dass die 5S Methode nicht zu strenge oder unflexible Standards enthält. Dies würde die Kreativität und Flexibilität der Mitarbeiter einschränken.
Kaizen
Kaizen bedeutet sinngemäß „Veränderung zum Besseren“ und ist eine Methode japanischen Ursprungs, die darauf abzielt, durch kleine, kontinuierliche Verbesserungen die Effizienz, Qualität und Produktivität von Prozessen zu steigern. Dabei werden alle Mitarbeiter eines Unternehmens, unabhängig von ihrer Hierarchieebene, aktiv in Verbesserungsprozesse einbezogen.
Kaizen hat den Vorteil, dass durch die ständige Identifikation und Beseitigung von Verschwendung nicht nur Arbeitsabläufe optimiert und Ressourcen besser genutzt werden, sondern damit einhergehend auch die Kosten gesenkt und die Effizienz gesteigert wird.
Kaizen schafft ein Umfeld, in dem Unternehmen durch regelmäßige kleine Veränderungen schnell auf Marktveränderungen und neue Anforderungen reagieren. Gleichermaßen werden Innovationen gefördert, da die Mitarbeitenden ermutigt werden, kreative Lösungen für bestehende Probleme zu finden. Das hat eine steigende Zufriedenheit der Mitarbeiter zur Folge.
Nachteilig ist Kaizen vor allem aufgrund ihres Zeitaufwands. Die Ergebnisse von Kaizen zeigen sich oft erst langfristig, was in schnelllebigen Geschäftsumfeldern als nachteilig empfunden wird. Auch die Implementierung von Kaizen erfordert einen erheblichen initialen Aufwand an Zeit und Ressourcen, insbesondere für Schulungen und die Etablierung einer Kaizen-Kultur. Kaizen erfordert eine kontinuierliche Überwachung und Anpassung. Auch dies führt langfristig zu einer Belastung der Ressourcen.
Just in Time (JIT)
Just-in-Time (JIT) ist ein Produktions- und Lieferkonzept, das darauf ausgerichtet ist, Materialien und Waren genau dann zu liefern, wenn sie benötigt werden, um Lagerbestände zu minimieren.
Da bei dieser Methode Materialien und Produkte nur bei Bedarf bestellt und geliefert werden, liegen die Vorteile klar auf der Hand: Zum einen verringern sich die Kosten für Lagerhaltung und die Risiken von Überbeständen und zum anderen erhöht sich durch die genaue Abstimmung von Lieferzeiten und Produktionsabläufen die Effizienz des gesamten Produktionsprozesses.
Unternehmen können schnell auf Veränderungen in der Nachfrage reagieren und Produktionspläne entsprechend anpassen, was eine größere Flexibilität im Produktionsprozess ermöglicht.
Just-in-Time hat allerdings den Nachteil, dass sie einen hohen Planungs- und Koordinationsaufwand einfordert. Eine enge Zusammenarbeit und Zuverlässigkeit der Lieferanten sind unabdingbar. Die Methode ist daher sehr risikoreich. Jede Verzögerung oder Störung in der Lieferkette kann die gesamte Produktion beeinträchtigen.
Total Minute Exchange of Dies (SMED)
Single Minute Exchange of Dies (SMED) zielt auf ein drastisches Reduzieren der Rüstzeiten (Umrüstzeiten) von Maschinen und Anlagen ab. Der Wechsel der Werkzeuge und Vorrichtungen soll so optimiert werden, dass er in weniger als zehn Minuten (also in einstelligen Minuten, „Single Minute“) durchgeführt werden kann.
Durch die Verkürzung der Rüstzeiten wechseln Maschinen und Anlagen schneller von einem Produktionslauf zum nächsten, was den klaren Vorteil mit sich bringt, dass die Maschinenverfügbarkeit und die Produktionseffizienz erhöht werden. Unternehmen können so flexibler auf Änderungen der Nachfrage reagieren, was zu einer besseren Anpassung an Kundenanforderungen führt. Außerdem werden die Bestände an Zwischen- und Endprodukten reduziert und damit die Lagerhaltungskosten gesenkt.
Doch es gibt auch Nachteile. Bei Single Minute Exchange of Dies (SMED) entstehen am Anfang erhebliche Kosten für die Implementierung. Schulungen, Prozessanalysen und möglicherweise neue Ausrüstungen sind erforderlich. Außerdem sind nicht alle Maschinen und Prozesse gleichermaßen für SMED geeignet.
Value Productive Maintenance (TPM)
Das Ziel von Total Productive Maintenance (TPM) ist es, die Effektivität und Effizienz von Produktionsanlagen durch präventive und vorausschauende Wartungsmaßnahmen zu maximieren. TPM strebt die vollständige Einbeziehung aller Mitarbeiter in die Wartungsprozesse an.
Die Methode bringt einige Vorteile, unter anderem dass durch die präventive Wartung Stillstandzeiten minimiert und gleichzeitig Produktionsleistung maximiert werden. Dies hat auch zur Folge, dass sich die Lebensdauer der Anlagen verlängert. Die gewarteten Maschinen funktionieren optimal, die Qualität der produzierten Güter steigt und das Risiko von Maschinenfehlern und Unfällen wird reduziert.
Von Nachteil ist, dass Total Productive Maintenance einen hohen Aufwand an Koordination und Planung von präventiven Wartungsmaßnahmen verlangt. Um die Effizienz von TPM aufrechtzuerhalten, sind kontinuierliche kosten- und zeitaufwändige Schulungen und Weiterbildungen der Mitarbeiter erforderlich.
Value Stream Mapping (VSM)
Value Stream Mapping (VSM) dient dazu, alle Schritte eines Produktionsprozesses visuell darzustellen. Das Ziel dieser Methode ist es, den Fluss von Materialien und Informationen von der Auftragserteilung bis zur Lieferung an den Kunden zu analysieren und zu optimieren.
Vorteile sind klar: Durch die klare und umfassende Visualisierung des gesamten Produktionsprozesses können sowohl wertschöpfende als auch nicht-wertschöpfende Aktivitäten (Verschwendung) innerhalb des Prozesses identifiziert werden. So erhält das Unternehmen die optimale Grundlage für Verbesserungsmaßnahmen. Diese Methode fördert auch eine bessere Kommunikation und Zusammenarbeit zwischen verschiedenen Abteilungen und Teams, da alle Beteiligten ein gemeinsames Verständnis des gesamten Prozesses und der bestehenden Probleme entwickeln.
Ein Nachteil von Value Stream Mapping ist, dass die Methode zu einer statischen Sicht auf Prozesse führen kann, die dynamische und schnell wechselnde Umgebungen nicht ausreichend abbildet
Wie lässt sich eine Lean Production im Unternehmen entwickeln?
Die Entwicklung einer Lean Production im Unternehmen erfordert einen systematischen und strukturierten Ansatz, der mehrere Phasen und Initiativen umfasst.
Das sind die wesentlichen Schritte zur Implementierung von Lean Production in einem Unternehmen:
Verständnis
Im ersten Schritt der Entwicklung einer Lean Production muss die Unternehmensführung die Lean-Prinzipien unterstützen und aktiv vorantreiben. Gleichzeitig ist es wichtig, dass die Mitarbeitenden ein Verständnis für die Implementierung der Lean Production entwickeln. An dieser Stelle ist zu empfehlen, direkt einen Berater oder Lean-Experten hinzuzuziehen, um den Prozess zu unterstützen und mit Hilfe von Best-Practice-Beispielen das Verständnis einer Lean Production zu erlangen.
Analyse
Der zweite Schritt ist eine ausführliche Analyse des Ist-Zustandes. Hierzu sollen alle Schritte im Produktionsprozess identifiziert und dokumentiert werden. Detaillierte Prozessflussdiagramme helfen bei der optimalen Visualisierung des aktuellen Produktionsprozesses. Regelmäßige Besuche der Produktionsstätten durch das Management (Gemba Walks) dienen dazu, direkt vor Ort Verbesserungsmöglichkeiten zu erkennen. In diesem Zusammenhang soll auch die Verschwendung im Produktionsprozess identifiziert werden.
Die sieben Arten der Verschwendung (Muda) sind:
- Überproduktion
- Wartezeiten
- Transport
- Überbearbeitung
- Bestände
- Bewegungen
- Defekte
Verbesserungsplan
Im dritten Schritt sind gemeinsam mit den Mitarbeitern mittels Kaizen-Workshops konkrete Verbesserungsmaßnahmen zu erarbeiten. Der PDCA-Zyklus (Plan-Do-Check-Act) hilft bei der Problemlösung und Prozessverbesserung durch das systematische Planen, Durchführen, Überprüfen und Handeln. An dieser Stelle ist es wichtig, Standardarbeitsanweisungen (Standard operating procedures; SOPs) zur Sicherstellung konsistenter Arbeitsabläufe zu entwickeln und zu etablieren.
Implementierung
Im vierten Schritt werden die bereits oben beschriebenen Lean-Methoden implementiert. 5S, Just-in-Time (JIT), Kaizen, Single Minute Exchange of Dies (SMED), Total Productive Maintenance (TPM), Value Stream Mapping (VSM).
Überwachung
Um den Erfolg der Lean Production in einem Unternehmen messen und sichern zu können, muss der Fortschritt im fünften Schritt überwacht werden. Dafür ist es entscheidend, Kennzahlen bzw. Key Performance Indicators (KPIs) festzulegen, anhand derer der Fortschritt gemessen und Verbesserungsmöglichkeiten erkannt werden. Innerhalb regelmäßiger Audits soll die Einhaltung der Lean-Prinzipien überprüft und der erzielte Fortschritt bewertet werden.
Langfristigkeit
Abschließend ist eine langfristige Strategie zur kontinuierlichen Verbesserung und Anpassung der Lean-Prinzipien an sich verändernde Bedingungen im Unternehmen zu entwickeln. Durch das Zusammenwirken dieser systematischen Schritte wird Lean Production erfolgreich in ein Unternehmen implementiert.
Welches sind die zentralen Produktionsfaktoren der Lean Production?
Die sieben Produktionsfaktoren der Lean Production sind:
- Menschliche Ressourcen
- Materialien
- Maschinen und Technologien
- Methoden und Prozesse
- Informationen
- Arbeitsplatzgestaltung
- Kundenzufriedenheit
Die Produktionsfaktoren der Lean Production sind eng miteinander verknüpft und müssen im Einklang optimiert werden, um die Vorteile einer schlanken Produktion voll auszuschöpfen.
Menschliche Ressourcen
Die Lean Production legt großen Wert auf Teamarbeit, Schulung, kontinuierliche Verbesserung (Kaizen) und die proaktive Mitarbeit durch Mitarbeiter. Jeder Mitarbeiter soll motiviert werden, seine eigenen Ideen und Meinungen einzubringen. Darüber hinaus spielen die Führungskräfte eine entscheidende Rolle in einer funktionierenden Lean-Kultur. Nur durch ihre Unterstützung und Vorbildfunktion kann Lean Production im Unternehmen erfolgreich sein.
Materialien
Ein zentraler Produktionsfaktor der Lean Production sind Materialien bzw. Güter und Produktionsmittel. Ihre Bestände sollen auf ein Minimum reduziert werden, damit die Lagerkosten gesenkt und die Flexibilität erhöht werden. Alle produzierten Güter sollen von hoher Qualität sein, um Fehler und Nacharbeit zu minimieren.
Maschinen und Technologien
Die Lean Production erfordert den Einsatz moderner und effizienter Maschinen, die wartungsfreundlich und flexibel einsetzbar sind.
Methoden und Prozesse
Die Minimierung von Verschwendung sowie die kontinuierliche Optimierung von Produktionsprozessen sind der Kern der Lean Production. Die Wertströme im Unternehmen müssen analysiert werden, um Verschwendung zu erkennen und zu eliminieren. Standardisierte Arbeitsanweisungen (SOPs) helfen bei der Sicherstellung konsistenter und effizienter Abläufe. Grundsätzlich soll sich eine Kultur der kontinuierlichen Verbesserung etablieren, in der alle Mitarbeiter ständig nach Verbesserungsmöglichkeiten suchen.
Informationen
Lean Production erfordert ein visuelles Management zur Unterstützung der Produktionsprozesse und zur Verbesserung der Transparenz. Hierbei kann optimal mit Schaubildern, Kanban-Boards und Andon-Systemen gearbeitet werden. Außerdem werden Informationen in Form von Leistungsdaten und Schlüsselkennzahlen (KPIs) gesammelt und analysiert, um Fortschritte zu messen und Entscheidungen zu treffen.
Arbeitsplatzgestaltung
Insbesondere 5S dient der Optimierung der Arbeitsorganisation und Arbeitsplatzsauberkeit. Außerdem ist der Arbeitsplatz unter ergonomischen Gesichtspunkten zu gestalten, um die Gesundheut und Arbeitsfähigkeit der Mitarbeiter zu erhalten.
Kundenzufriedenheit
Die Lean Production fördert die Ausrichtung der Produktion an den Anforderungen und Erwartungen der Kunden. Das Unternehmen muss dazu in der Lage sein, schnell auf Änderungen in der Kundennachfrage und auf Marktbedingungen zu reagieren. Das Ziel ist die Erhöhung der Kundenzufriedenheit, auch um ressourcenfressende Reklamationen zu vermeiden.
Mit welchen Kennzahlen misst man den Erfolg von Lean Production
Um den Erfolg von Lean Production zu messen, werden verschiedene Kennzahlen verwendet, die Aufschluss über die Effizienz und Effektivität der Produktionsprozesse geben.
Die sieben wichtigsten Erfolgskennzahlen der Lean Production sind:
Lead Time (Lieferzeit)
Die Zeitspanne von der Auftragserteilung bis zur Auslieferung eines fertigen Produkts wird Lead Time genannt.
Anlagen von GREIF-VELOX optimieren und automatisieren Abfüllprozesse und Verpackungsprozesse. Beides reduziert die Lead Time erheblich.
Durchlaufzeit (Cycle Time)
Die Durchlaufzeit ist die Zeit, die ein Produkt benötigt, um einen bestimmten Produktionsprozess von Anfang bis Ende zu durchlaufen.
GREIF-VELOX-Anlagen verkürzen die Durchlaufzeit, indem sie schneller arbeiten und Engpässe in den Verpackungs- und Handlingprozessen beseitigen.
Durchsatz (Throughput)
Die Menge an Produkten, die in einem bestimmten Zeitraum produziert werden, wird als Durchsatz bezeichnet.
Durch die hohe Effizienz und Automatisierung der Anlagen von GREIF-VELOX werden mehr Produkte in kürzerer Zeit abgefüllt, abgesackt oder verpackt und bereitgestellt. Der Durchsatz wird so erhöht.
Auslastung (Utilization)
Auslastung bezeichnet den Prozentsatz der verfügbaren Produktionskapazität, der tatsächlich genutzt wird.
GREIF-VELOX-Analgen arbeiten kontinuierlich und effizient. So wird die Produktionskapazität optimal genutzt.
Fehlerrate (Error Rate)
Die Fehlerrate ist der Prozentsatz der produzierten Einheiten, die fehlerhaft sind.
Durch den Einsatz der GREIF-VELOX-Analgen wird die Fehlerrate in Unternehmen deutlich gesenkt. Die Anlagen arbeiten präzise sowie zuverlässig und minimieren auf diese Weise Fehler in den Verpackungsprozessen.
Wertschöpfungsgrad (Value-Added Ratio)
Der Wertschöpfungsgrad ist der Anteil der wertschöpfenden Zeit an der gesamten Produktionszeit.
Durch die Automatisierung und Effizienz der Anlagen von GREIF-VELOX wird der Wertschöpfungsgrad erhöht, da mehr Zeit für wertschöpfende Tätigkeiten und weniger Zeit für nicht-wertschöpfende Aktivitäten aufgewendet wird.
Overall Equipment Effectiveness (OEE)
Die Kennzahl zur Messung der Produktivität einer Anlage, die sich aus Verfügbarkeit, Leistung und Qualität zusammensetzt, wird als Overall Equipment Effectiveness (OEE) bezeichnet.
GREIF-VELOX-Anlagen verbessern die OEE, indem sie hohe Verfügbarkeit (weniger Ausfallzeiten), hohe Leistung (schnelle und effiziente Verarbeitung) und hohe Qualität (geringe Fehlerrate) gewährleisten.
Welche Bedeutung hat Lean Production für Unternehmen im globalisierten Produktionswettbewerb?
Unternehmen implementieren Lean Production, um im globalen Produktionswettbewerb konkurrenzfähig zu bleiben, Kosten zu senken, die Effizienz zu steigern und auf die sich ständig ändernde Marktbedingungen flexibel zu reagieren.
Abfüllanlagen und Verpackungssysteme von GREIF-VELOX helfen Unternehmen bei der Einführung und Umsetzung einer Lean Production in ihrem Produktionsbetrieb. Insbesondere die Parameter Produktionsgeschwindigkeit, Mess- bzw. Abfüllgenauigkeit und Produktionssicherheit werden durch GREIF-VELOX-Anlagen verbessert.
Beispiel: Lean Production in der Chemie-Branche
In der Chemie-Branche sind maximale Präzision, Sicherheit und Sauberkeit die Hauptanforderungen an alle produktionstechnischen Abfüllprozesse. Die Lean-Methode „Just in Time“ unterstützt präzises Arbeiten, indem sie die Materialverfügbarkeit genau mit dem Produktionsbedarf synchronisiert. So kann ein Unternehmen seine Lagerbestände reduzieren und die Flexibilität erhöhen.
Kaizen sorgt für eine kontinuierliche Verbesserung der Prozesse. Daraus resultieren eine geringere Fehlerquote und eine höhere Fertigungspräzision. Darüber hinaus begünstigt die Lean-Methode Poka Yoke die Produktionspräzision, indem sie durch Fehlervermeidungstechniken sicherstellt, dass Produktionsprozesse automatisch optimiert werden, bevor Fehler auftreten.
Der Sicherheitsaspekt ist in der chemischen Industrie von besonderer Bedeutung. Lean Production fördert standardisierte Prozesse und kontinuierliche Verbesserungen und sorgt damit für mehr Sicherheit. Durch Lean-Methoden werden Störfälle und Unfälle mittels strenger Prozesskontrollen und vorbeugender Instandhaltung minimiert. Diese Maßnahmen erhöhen die Sicherheit der Mitarbeiter.
Chemie- und Lebensmittel-Branche
Innovative Feststoff-Abfüllanlage für ICL Ladenburg
Die Feststoff-Abfüllanlage von GREIF-VELOX bei ICL Ladenburg führte zu einer signifikanten Senkung der Reklamations- und Reinigungskosten, die ursprünglich durch fehlerhaft verschweißte Säcke verursacht wurden. Diese Kostenproblematik, die jährlich mindestens 20.000 Euro betrug, wurde durch die Einführung des ValvoDetect am Luftpacker BVP radikal verbessert. ValvoDetect sorgt mit seinen optischen Sensoren dafür, dass nur korrekt positionierte Säcke verschweißt werden, indem es fehlerhaft aufgesteckte Säcke vor dem Verschweißen erkennt und aussortiert.
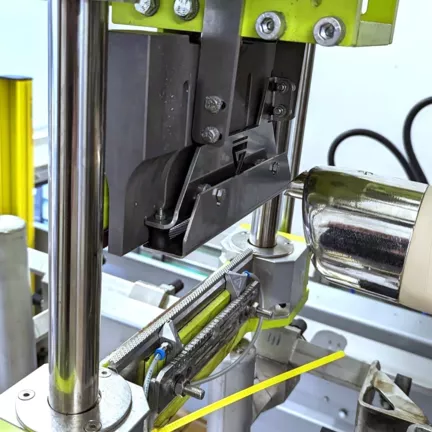
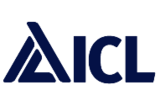
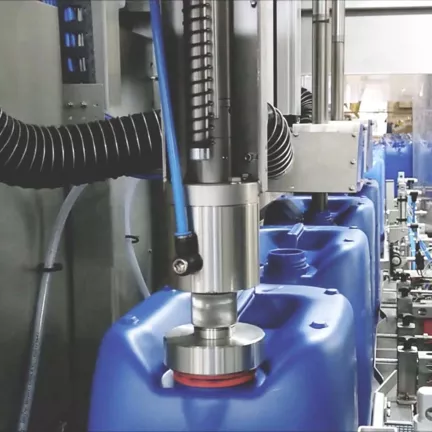
Chemie-Branche
Wasserstoffperoxid-Abfüllanlage für Evonik
Unsere Abfüllanlage beim Chemieunternehmen Evonik führte zu einer eindrucksvollen Steigerung der Abfüllgeschwindigkeit um 50 Prozent. Zusätzlich verbesserten wir die Produktsicherheit erheblich durch die Implementierung von fortschrittlichen Kontaminationsschutzmaßnahmen, die in einem hochautomatisierten Abfüllsystem für Wasserstoffperoxid integriert wurden, wodurch nicht nur die Effizienz, sondern auch die Sicherheit am Arbeitsplatz gesteigert wurde.
Regelmäßiges Reinigen verbessert die Sauberkeit und Ordnung, die in den Unternehmen der Chemie-Branche von hoher Bedeutung sind. Lean Production unterstützt durch die Anwendung der 5S-Methode die Einführung und strikte Einhaltung standardisierter Reinigungsverfahren.
Durch kontinuierliche Verbesserungsprozesse (Kaizen) werden ständig potenzielle Schwachstellen in Bezug auf Sauberkeit identifiziert und behoben. Der Einsatz von Visual Management kann Sauberkeitsstandards klar kommunizieren und überprüfen. Farblich markierte Bereiche, Checklisten und visuelle Anleitungen helfen, die Einhaltung der Reinigungsstandards zu gewährleisten. Sichtbare Kontrollpunkte und regelmäßige Inspektionen machen es einfacher, den Sauberkeitsstatus in Echtzeit zu überwachen und sicherzustellen.
Der Einsatz von Poka Yoke (Fehlervermeidung) sorgt dafür, dass Anlagen automatisch gereinigt werden, um menschliches Versagen zu vermeiden. Lean Production betont die Bedeutung der Dokumentation aller Reinigungsvorgänge. Eine lückenlose Dokumentation hilft dabei, die Einhaltung von Sauberkeitsstandards nachzuweisen und bei Inspektionen oder Audits bereit zu sein.
Beispiel: Lean Production in der Lebensmittel-Branche
Für die Lebensmittel-Branche müssen Abfüll-Lösungen hygienisch, genau und zuverlässig sein. Nur so können die spezifischen Anforderungen dieser Branche zuverlässig bewältigt werden. Hygienische Abfüllprozesse verhindern die Kontamination von Lebensmitteln mit schädlichen Bakterien, Viren, Parasiten und Chemikalien, die Lebensmittelvergiftungen und ernste Gesundheitsprobleme verursachen.
Außerdem gewährleistet Hygiene bei der Abfüllung das Einhalten der gesetzlichen Anforderungen. Die Lean Production fördert die Einführung und Einhaltung von standardisierten Reinigungsverfahren, so dass die Hygiene aller Abfüllanlagen gesichert ist.
Die 5S-Methode sorgt in der Lebensmittel-Branche dafür, dass
- unnötige Materialien und Werkzeuge aus dem Arbeitsbereich entfernt werden, um die Ansammlung von Schmutz zu vermeiden,
- die Arbeitsplätze organisiert sind, um sicherzustellen, dass Reinigungsgeräte und -mittel leicht zugänglich und einsatzbereit sind,
- durch ein regelmäßiges und systematisches Reinigen der Arbeitsbereiche und Maschinen die Hygiene gewährleistet ist,
- Standards für Sauberkeit und Ordnung eingeführt werden und
- eine nachhaltige Aufrechterhaltung der Sauberkeitsstandards durch regelmäßige Inspektionen und Schulungen gegeben ist.
Durch kontinuierliche Verbesserungsprozesse (Kaizen) werden in der Lean Production potenzielle Hygienerisiken identifiziert und behoben. Der Einsatz von Visual Management dient darüber hinaus der klaren Kommunikation und Überprüfung von Hygienestandards. Dank der automatischen Überwachungssysteme (Poka Yoke) werden Verunreinigungen erkannt und angezeigt.
Lebensmittel-Branche
Absackanlage für GoodMills Deutschland
Beim Lebensmittelproduzenten GoodMills Deutschland konnten wir die Verpackungseffizienz dank unserer Anlagen signifikant um 100 Prozent steigern. Zudem maximierten wir die Genauigkeit der Abfüllprozesse, wodurch die Produktionsleistung auf bis zu 400 Säcke pro Stunde verdoppelt wurde, während gleichzeitig durch den Einsatz unseres Bruttopneumatikpackers BVPV 4.40 der Reinigungsaufwand und die Umrüstzeiten minimiert wurden.
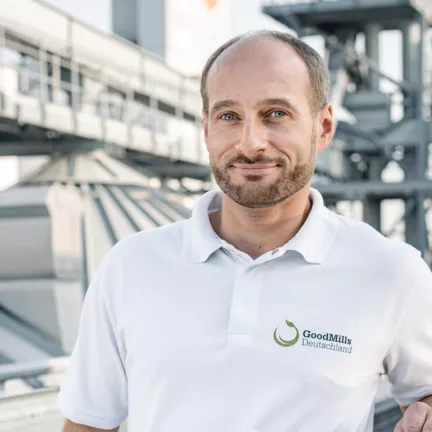
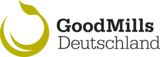
Beispiel: Lean Production in der Petrochemie
In der Petrochemie-Branche sind viele Produkte toxisch, brennbar, anderweitig gefährlich und haben oft komplexe chemische Eigenschaften, die spezielle Materialien und Anlagen- sowie Fertigungskonstruktionen erfordern.
Die Abfüll-Lösungen müssen daher robust, leistungsstark und anpassungsfähig sein, um die spezifischen Bedürfnisse dieser Branche zu bewältigen. Lean Production unterstützt die hohen Anforderungen und Herausforderungen für robuste und leistungsstarke Abfüllanlagen und Verpackungssysteme der Petrochemie durch „Total Productive Maintenance“-Strategien.
Diese Strategien stellen sicher, dass die Abfüllanlagen leistungsstark bleiben, in dem sie regelmäßig gewartet werden. Die Einbeziehung der Maschinenbediener in die Wartungsprozesse erhöht die Zuverlässigkeit der Anlagen, da Probleme frühzeitig erkannt und behoben werden.
Darüber hinaus fördert Kaizen die kontinuierliche Suche nach Verbesserungsmöglichkeiten in den Abfüllprozessen, was leistungsstarke Abläufe ermöglicht. Lean Production vermeidet unnötige Bestände durch die Synchronisation von Produktion und Nachfrage. So wird die Leistungsfähigkeit der Abfüllprozesse erhöht. Das Visual Management schafft die notwendige Transparenz im Produktionsprozess, um Probleme leichter erkennen und beheben zu können und somit eine konstante Leistung zu gewährleisten.
Die in der Petrochemie erforderliche Anpassungsfähigkeit von Abfüllanlagen und Verpackungssystemen fördert die Lean Production durch die Implementierung von Just-in-time-Prinzipien. Unternehmen können ihre Produktion schnell an wechselnde Nachfragebedingungen anpassen, indem sie Materialien und Produkte genau zur richtigen Zeit bereitstellen.
Lean Production sorgt dafür, dass durch SMED-Techniken die Rüstzeiten erheblich reduziert werden, wodurch der Abfüllprozess schnell zwischen verschiedenen Produkten umgestellt werden kann. Durch die Standardisierung der Umrüstprozesse können Rüstvorgänge effizient und konsistent durchgeführt werden, was die Anpassungsfähigkeit erhöht. Der Einsatz skalierbarer Technologien, die leicht an unterschiedliche Produktionsvolumina angepasst werden können, ohne signifikante Änderungen an der Infrastruktur vornehmen zu müssen, erhöht die Anpassungsfähigkeit enorm.
Wo lassen sich Lean-Konzepte und Lean-Maßnahmen außerhalb der Produktion einsetzen?
Lean Production konzentriert sich hauptsächlich auf die Optimierung von Produktionsprozessen durch die Minimierung von Verschwendung und die Maximierung der Effizienz. Diese Prinzipien haben sich im Bereich Fertigung von Produktionsbetrieben als äußerst erfolgreich erwiesen und zu erheblichen Verbesserungen insbesondere in der Produktivität und Qualität geführt, wie die obigen Beispiele aus der Chemie-Branche und Lebensmittel-Branche exemplarisch offengelegt haben.
Jedoch beschränkt sich die Anwendung der Lean-Prinzipien nicht nur auf die Fertigung bzw. Produktion. Um die volle Wirkung von Lean zu entfalten, müssen diese Prinzipien auf die gesamte Organisation ausgedehnt werden. Hier kommt Lean Management ins Spiel. Lean Management überträgt die Konzepte von Lean Production auf alle Geschäftsbereiche und Prozesse innerhalb eines Unternehmens.
Was ist Lean Management?
Während Lean Production also auf die Fertigung abzielt, strebt Lean Management eine umfassende Kultur der kontinuierlichen Verbesserung und Effizienz im gesamten Unternehmen an. Es geht darum, Verschwendung in allen Formen zu eliminieren, sei es in der Verwaltung, im Kundenservice oder in anderen unterstützenden Funktionen.
Durch die Umsetzung von Lean Management können Unternehmen eine ganzheitliche, schlanke und effiziente Organisation schaffen, die besser in der Lage ist, sich an Veränderungen anzupassen und nachhaltig wettbewerbsfähig zu sein.
Lean Management basiert auf denselben Prinzipien des Lean-Konzepts und erfordert daher die gleichen Prozessschritte: Identifikation von Wert aus Kundensicht, Wertstrom identifizieren, Fluss schaffen, Pull-System einführen und das Streben nach Perfektion, das Qualitätsmanagement, Mitarbeiterbeteiligung und -entwicklung, visuelles Management sowie Technologie und Automatisierung einschließt.