Factory Acceptance Tests (FAT)
Successful handover and installation of GREIF-VELOX systems for customers
STW Kautzmann
FAT of the VeloVac vacuum bagging system
As part of the factory acceptance test, the fully automatic VeloVac 2-spout vacuum bagging system demonstrated its impressive performance. The system, which was specially developed for STW Kautzmann GmbH, is designed as an integrated full-line solution and combines the processes of sealing, levelling and palletizing in one integrated system.
Project results and key figures
Output: The system achieves a capacity of 80 bags per hour - designed for 6.5 kg and 12.5 kg bags
Innovative technology: A new bag gripper enables flexible handling of varying bag formats
Process integration: The combination of automated sealing, levelling and subsequent palletizing significantly optimizes the packaging process
About the customer – STW Kautzmann GmbH
Schwarzwälder Textil-Werke Heinrich Kautzmann GmbH is a traditional family business from Schenkenzell in the Black Forest. With around 95 employees and over a century of experience in the development and production of high-quality fibers, STW has established itself as a leading specialist for fiber fillers, fiber short cuts, fibrides and pulp.
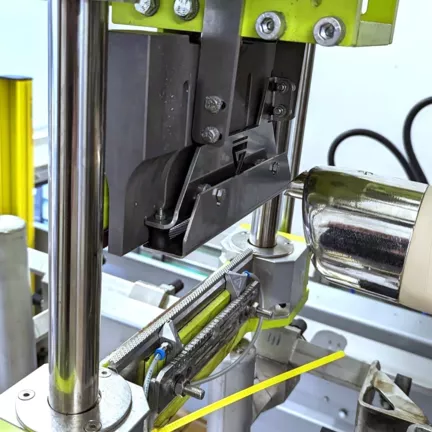
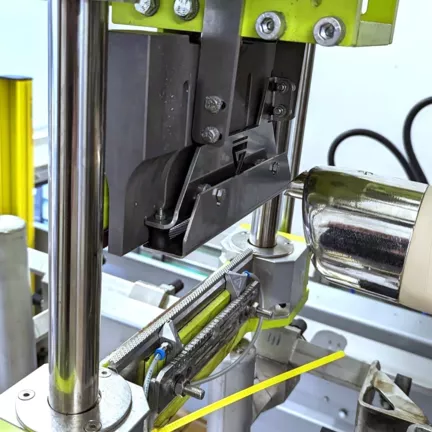
Schülke & Mayr
Factory Acceptance Test of the R-DOS-2W filling system
As part of the FAT, our customized R-DOS-2W filling system demonstrated its high efficiency in the manual filling of disinfectants. The GREIF-VELOX solution uses alternating operation of two integrated scales, enabling continuous and accelerated filling.
Results and Key Figures:
Double Efficiency: Optimized alternating operation of the two scales
Process Optimization: Faster, continuous manual filling process
About the Customer:
Schülke & Mayr is a traditional chemical company specializing in innovative disinfectants and hygiene products. The company represents the highest quality standards and continuous innovation in the chemical industry.
Allnex
Factory Acceptance Test of the A-DOS-P1 filling systems
As part of a successful FAT, two fully automated A-DOS-P1 filling systems were commissioned at the plant. The systems impress with a full-line solution that includes an integrated load securing system, robotic labeling for drums and IBCs, and ATEX certification.
Results and Key Figures:
Safety Standard: ATEX certification guarantees the highest safety
Automation: Integrated robotic labeling optimizes the process
Full-Line: Comprehensive solution with load securing
About the Customer:
Allnex is a leading global manufacturer of coating resins, producing innovative and reliable chemical industry products for various industries from architecture and automotive to protective clothing.
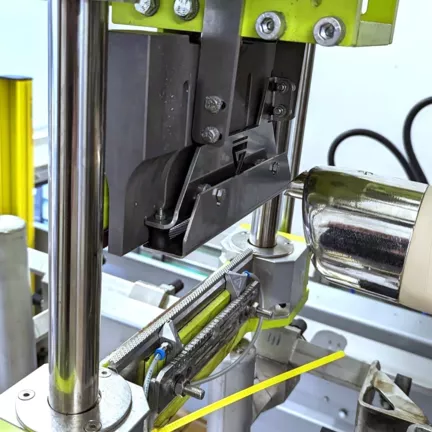
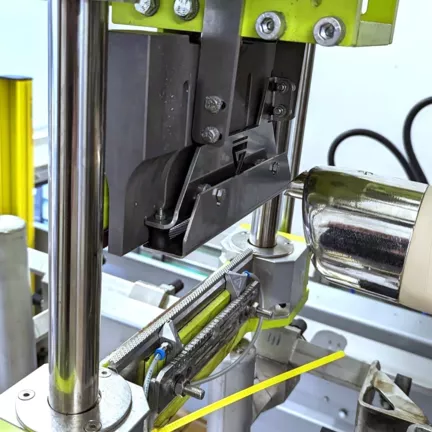
MÜNZING Emulsions Chemie & MÜNZING Micro Technologies
Factory Acceptance Test of the Full-Line filling system
The renowned manufacturer of specialty additives has approved a full-line solution as part of an FAT. The system includes two pneumatic packers (BVP), the Valvomat S1 applicator, and integrated conveyor technology - ideal for efficiently filling micronized wax products.
Results and Key Figures:
Integrated Solution: Combination of pneumatic packers, applicators, and conveyor technology
Efficiency: Optimized filling processes for micronized wax products
About the Customer:
MÜNZING Emulsions Chemie GmbH and MÜNZING Micro Technologies GmbH are among the leading providers of specialty additives. With innovative solutions and a strong focus on quality, they have a lasting impact on the chemical industry.
Daesang Corporation
Factory Acceptance Test of the Gross Pneumatic Packer BVPV
As part of the FAT, the Gross Pneumatic Packer BVPV was successfully approved in fourfold execution.
Results and Key Figures:
Food-Grade Components: Stainless steel pre-container in food-grade execution
Flexibility: Adaptation to various bag sizes
Safety: Integrated combo checker for rejection in case of incorrect weight or metal detection
Performance: Impressive capacity of 600 bags per hour
About the Customer:
Daesang Corporation is an internationally active manufacturer of leading South Korean food brands. The company stands for high-quality food ingredients and sets global standards in food technology.
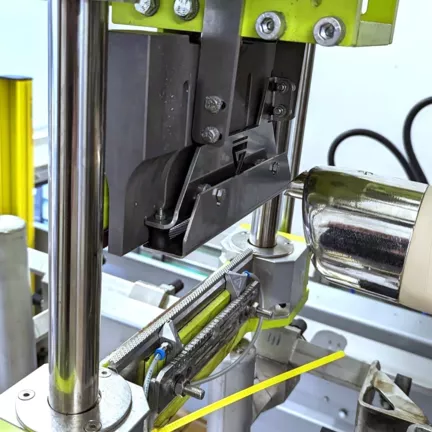
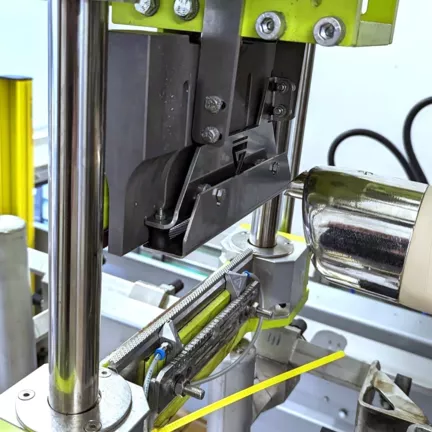
Symrise
Factory Acceptance Test of the Semi-Automatic R-DOS Filling Lines
As part of a successful FAT, two semi-automatic R-DOS filling lines were commissioned. With a filling capacity of up to 50 drums per hour, the "Aroma Molecules" business unit in Granada (Spain) will be efficiently served.
Results and Key Figures:
Process Optimization: Efficient integration into existing production workflows
Throughput: Up to 50 drums per hour
About the Customer:
Symrise is one of the world's leading companies in flavors, fragrances, and cosmetic ingredients. With innovative products and internationally oriented production facilities, Symrise continuously sets new standards in the cosmetics and food industries.
Cabot BV (Botlek)
Factory Acceptance Test of the Vacuum Packer VeloVac
The VeloVac vacuum packer was approved as a full-line solution as part of a successful FAT. The system enables dust-free bagging of ultra-light powders and thus meets the highest requirements in the production of carbon black and silica.
Results and Key Figures:
Dust-Free Bagging: Optimal conditions for ultra-light powders
Full-Line Concept: Integrated solution for efficient production processes
About the Customer:
Cabot BV is one of the world's largest manufacturers of carbon black and silica. The company is internationally known for its leading technologies and product developments in the field of industrial fine powders.
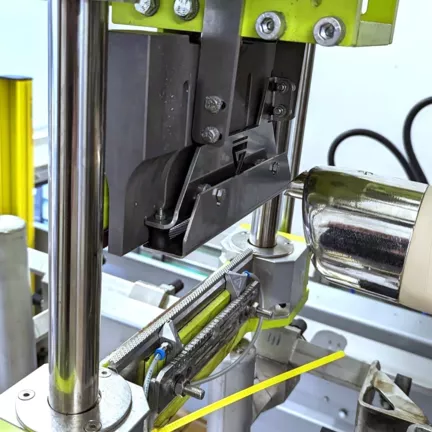
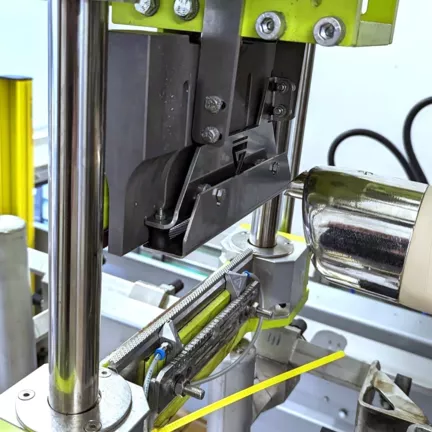
Rhenus Lub
Factory Acceptance Test of the Small Packaging Filling System S-Dos-E
As part of an FAT, the small packaging filling system of type S-Dos-E was successfully approved. The system ensures precise, efficient, and reliable filling of lubricating greases and oils and integrates seamlessly into the existing system.
Results and Key Figures:
Precision: Reliable filling of lubricants
Modernization: Upgrading an existing system for optimized processes
About the Customer:
Rhenus Lub is a successful traditional company in the field of industrial lubricants. The company stands for future-oriented product developments and high-quality standards in fluid management and specifically in lubricant technology.