The customer

Omnisal GmbH produces high-quality phosphates and phosphate blends that are used by companies in the food industry in over 85 countries. Its products are used in particular in the meat, seafood, cheese and dairy products, baked goods and wine sectors. Omnisal produces and processes the products at the Lutherstadt Wittenberg site in Saxony-Anhalt and, together with Fosfa a.s., is part of the FB HOLDING Group - the largest processor of yellow phosphorus in Europe.
The starting point
In view of long-term growth prospects in the global market for phosphorus and derivatives, the previous bagging system no longer met Omnisal's increasing requirements for efficiency and cleanliness. The outdated system could no longer cope with the growing production volumes and high hygiene requirements.
The request
Omnisal wanted to significantly increase the reliability, productivity, hygiene and bagging performance of production. The requirements included
- A fully automated system for safe and clean bagging of the different phosphate mixtures
- Integration of an existing filling system that was already filling 240 bags per hour
- Short downtimes and cleaning intervals during product changeovers to avoid interrupting the production flow
The solution
Omnisal opted for a full-line solution - a flexible, complete bagging system including state-of-the-art robotics and conveyor technology that bags the changing phosphate recipes fully automatically. The solution includes all the necessary components to hygienically and efficiently fill the bulk material into containers, label it and stack it on pallets ready for dispatch. Key elements of the solution:
- „Hygienic design“: All surfaces that come into contact with the product are made of stainless steel and fulfil the highest food processing requirements.
- Perfect coordination: All essential components - from the gripping tools to the robot programming - come from Greif-Velox and guarantee the highest quality and process reliability.
- High bagging capacity: The BVPV 4.40 fills powders, granulates, pellets or product mixtures with particle sizes between 50 µ and 12 mm into up to 240 bags or 12 FIBCs per hour. An integrated magazine ensures that the containers are stocked as required and labelled individually.
- Clean, dust-free bagging: The Aspiration Shield immediately absorbs any dust that escapes during the filling process, while the patented ValvoSeal ultrasonic sealing unit ensures a reliable and dust-free seal.
- Quality control: The ValvoDetect optical measuring system sorts out faulty or incorrectly sealed bags before palletising, preventing contamination of entire pallets and reducing complaint costs.
- Automatic palletising: The VeloPack four-axis palletising robot stacks the bags precisely and quickly, seals them, labels them and prepares them for dispatch.
- Reduced downtimes: Thanks to special emptying technology and an efficient wet cleaning function, cleaning times for product changes have been minimised by up to 80 percent.
The result: Cost savings and high process reliability at Omnisal
By using the new full-line bagging system, Omnisal is realising significant cost savings while increasing process reliability and product quality. The perfectly harmonised system components not only enable reliable production, but also offer potential for future expansions in the smart industry sector.
The end-to-end hygiene concept guarantees error-free and food-safe bagging, while all relevant process data can be recorded and evaluated for data-based optimisation.
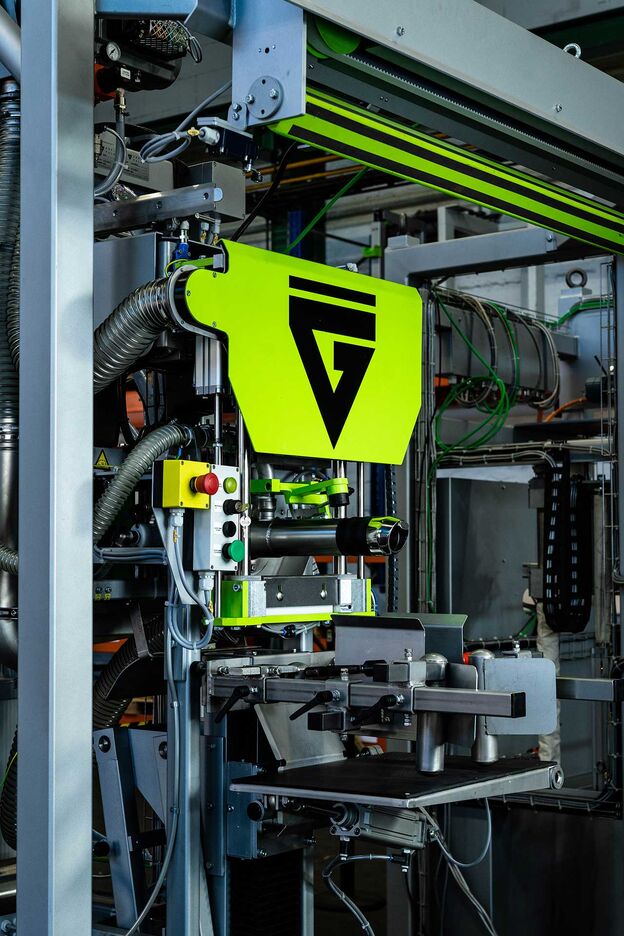
We were already very satisfied with the acceptance test at Greif-Velox in Lübeck. The system can now play to its strengths in day-to-day production.
DALIBOR KUCHAR,
Omnisal
Significant performance increase
Maximum process and product safety
Savings in personnel costs
Reduction in cleaning and complaint costs
Minimisation of downtimes during product changes