Our system and equipment for optimum load securing
Automatic palletising
VeloPack robot
Highly efficient palletising with precision
The VeloPack robot enables fully automatic palletising and depalletising of bags, drums, canisters and buckets. Thanks to its modular configuration, it can be flexibly adapted to your production lines.
Performance: Up to 1,200 bags or 140 drums per hour
Carrying capacity: Up to 400 kg for heavy containers
Flexibility: 4- to 6-axis robots, multiple palletising of different lines
Additional options: Gripping tool for pallet and cover sheet handling
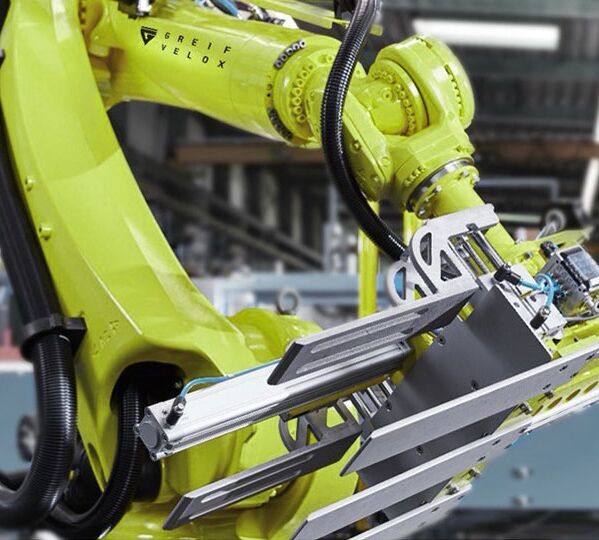
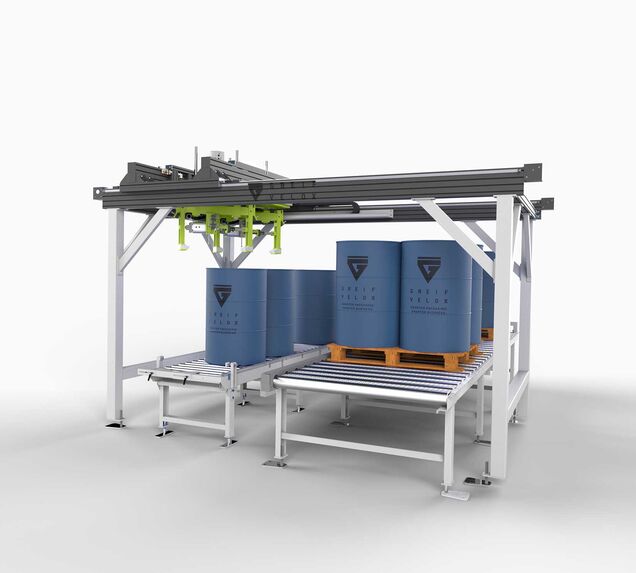
Portal palletizer
Fully automatic for demanding formats
Specially developed for drums, hobbocks and canisters, the gantry palletiser integrates seamlessly into conveyor systems.
Versatility: Can be used as a gripper, vacuum or push palletizer
Integration: Can be combined with all conveyor technology elements
Safety: Minimises manual intervention and increases operational safety
VELOFLEXLABELER
Efficient and reliable labeling for various container shapes
The compact design of the VeloFlexLabeler facilitates integration into existing production lines, while the positioning of labels can be freely adjusted regardless of the size or shape of the containers. This makes the system ideal for industries such as chemicals, food, and logistics.
Precise Labeling: Ensures flawless labeling even at high production speeds
Redundant Printing Systems: Prevent downtime and adhesive failures
Versatile Application Options: Allows for the application of tamper-evident seals or static warnings
Maximum Flexibility: Choice of printing and dispensing systems and adaptability to various label sizes

Load securing technologies
Stretch wrapper
Stabilization under extreme conditions
Fixes pallets with up to 80 wraps per hour and offers special solutions for dust- or rain-proof securing.
Performance: Up to 80 pallets per hour
Special functions: Special films for extreme transport requirements
Advantage: Prevents slipping and tipping over
Corner and edge protection systems
Automatic product protection
Automatically integrates protective materials to prevent damage to packaging.
Application: Ideal for sensitive containers such as chemical canisters or food cartons
Efficiency: Reduces manual rework by 30%
Combi-Checker
Quality assurance in real time
Checks weight and detects metal particles so that only flawless packaging is forwarded.
Function: Prevents incorrect loads and complaints
Cost savings: Reduces reject rate by up to 15%
Cover sheet handling
Automatic protection for your load
Flexible solutions for placing cover sheets - by robot gripper or external dispenser.
Options: External cover sheet dispenser, film applicator
Advantage: Reduces manual work steps by 20%
Conveying and handling technology
Pallet conveyor technology
Safe transport and transfer
Customized solutions with roller and chain conveyors, corner transfer units and pallet lifts.
Modularity: Easy integration into existing lines
Throughput: Minimises downtimes thanks to automated removal
Empty plate handling
Increased efficiency through automation
Robots or external magazines handle empty pallets flexibly - with / without film applicators.
Flexibility: Access to multiple palletizing stations in one line
Time saving: Reduces manual handling by 50%
Bag equalization
Optimal preparation for palletizing
Shapes bags using vibrating plates, pressing stations or ironing belts for even stacking.
Precision: Uniform distribution of bulk material in the bag
Methods: Ironing bands, vibration plates, pressing stations, torture stretches
Application: Ideal for food and chemical bags
In addition to individual systems, GREIF-VELOX offers turnkey full-line systems - everything from a single source. These tailor-made complete solutions combine conveyor technology, palletizing and load securing in one system.
They can be adapted to the available space and production volumes, and can be easily expanded to meet increasing demand or new requirements.
Advantages of production automation with GREIF-VELOX load securing
Success factors for the chemical, petrochemical and food industries
Clean
Precise handling techniques minimize contact between products and the environment - ideal for the chemical and food industries to avoid contamination
Automatic
Fully automatic processes reduce manual intervention by 70% and increase operational reliability
Efficient
Maximize your throughput with 1,200 bags per hour (VeloPack) and 80 pallets / hour (stretch wrapper)
Safe
Integrated safety features such as corner and edge protection systems reduce damage rates by 25% and protect employees
Cost-efficient
Combined checker and automated quality control reduce complaints and rejects by 15%
Specific
Tailor-made solutions - e.g. 6-axis robots or gantry palletizers for drums - adapt precisely to your pack requirements
Precise
Highly developed control technologies position bags and drums with a tolerance of ±2 mm
Flexible
Modularity and fast changeover times enable switching between product lines in under 30 minutes
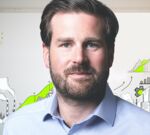
For over 60 years, GREIF-VELOX has been firmly established in the international markets of the chemical, food and petrochemical industries and is valued by customers and partners for its customized filling and packaging solutions, reliability and innovative strength.
Quote: Managing Director Sebastian Pohl
Became the market leader within just a few years
Our experience is reflected in a large number of projects, such as the increase in packaging efficiency at GoodMillsGroup, where we were able to effectively double production output, and the implementation of our ValvoDetect system at ICL Ladenburg, which led to a significant reduction in complaint and cleaning costs.
These and many other case studies demonstrate our ability to respond to a wide range of industry requirements and provide customized, effective solutions. If you would like to see specific examples of our work or gain a deeper insight into our bespoke installations, please contact the appropriate contact person.