Automation of production in Industry 4.0
In Industry 4.0, production automation plays a central role. Industry 4.0 involves the networking of machines and systems to create an intelligent production facility in which processes are controlled autonomously and in real time.
In this environment, automation enables the integration of modern technologies that not only make production processes more efficient and flexible, but also better adapt them to individual requirements. In industrial production , many processes, from manufacturing to logistics, can thus be automated.
The automation pyramid provides a structure that systematically organises these processes, while automation technology enables their implementation. In this way, production automation reduces waste in manufacturing processes and maximises production efficiency.
GREIF-VELOX uses semi-automatic and fully automatic systems specialising in material filling and packaging to automate production in Industry 4.0. These systems include high-precision dosing and weighing technologies as well as autonomous systems for filling, packaging and material transport. They also include advanced control systems and sensor technology that enable real-time monitoring and control of production processes.
The following text examines the role of automation in Industry 4.0 and analyzes its importance for modern industrial production.
What is automation?
Automation in industrial production refers to the use of technologies and systems to carry out production processes autonomously and without constant human intervention, with the aim of increasing efficiency, quality and consistency.
According to DIN 19233, automation technology is characterized by the use of technical systems and artificial means to control and run processes in such a way that they function largely independently.
Automation includes both the control and regulation of processes in various industrial processes. Plants and production systems are able to carry out certain tasks independently by using predefined instructions, algorithms or programming. The electrical engineering dictionary DIN IEC 60050-351 supplements this definition by describing that a process or technical device is described as "self-acting" or "automatic" if this process or device operates under specified conditions without the need for direct human intervention. This means that the systems are able to react to specific situations and parameters, make decisions and carry out actions independently. This ability to be autonomous is a key aspect of automation technology, as it significantly increases efficiency and consistency in production while minimizing human error sources.
In the process industry, which focuses on the manufacture of products through chemical, physical or biological processes, automation enables the precise control and monitoring of complex processes. This is particularly important in industries such as the chemical, food, pharmaceutical and petrochemical industries in order to meet high quality standards and regulatory requirements.
A concrete example of the importance of automation is the fully automatic filling system A-DOS-P1 from GREIF-VELOX. This system can fill up to 40 drums or 15 IBCs per hour and ensures maximum precision and reliability. With functions such as automatic bunghole detection and the integrated capping mechanism, the A-DOS-P1 not only increases production efficiency, but also reduces manual intervention and thus the risk of operating errors. Such innovative technologies show how automation not only increases process reliability, but also improves production efficiency.
6 phases of industrial automation
The following six phases of automation describe the gradual transition from manual and mechanized processes to fully networked and self-organizing systems that are characteristic of modern Industry 4.0:
- Connectivity
In this initial phase, machines, devices and systems are mostly connected to each other via the Internet of Things (IoT). Connectivity enables the exchange of data between different systems and creates the basis for data-driven decisions. For example, IoT sensors are integrated into production systems and communication protocols such as OPC UA are introduced. - Data integration and transparency
The collected data is analyzed and visualized in real time (real-time dashboard for production monitoring) to create transparency over the entire production process. This phase makes it possible to monitor the condition of the equipment, identify weak points and increase efficiency. - Decentralized decision making
Intelligent systems such as automated control systems are introduced that are able to make decisions independently. These systems analyze the production data and adapt the processes without human intervention to perform optimizations. - Technical assistance systems
In this phase, people are supported by technical assistance systems that help them make decisions and solve problems. Systems such as augmented reality (AR) for maintenance work and AI-based decision support systems provide enhanced information and suggestions based on the analyzed data. - Self-organizing systems
Systems in this phase are able to organize and optimize themselves. Self-optimizing production lines that respond to varying order quantities and autonomous manufacturing cells that flexibly adapt to different product configurations can respond to changes in the environment or requirements and independently adjust their operating parameters. - Cyber-physical systems (CPS) and smart factories
The highest phase of automation in Industry 4.0 includes fully integrated and networked cyber-physical systems that operate in both the physical and virtual worlds. In smart factories, these systems interact autonomously and in a coordinated manner to optimize the entire value chain. Examples of this include fully autonomous manufacturing plants that optimize production processes in real time and integrated supply chains that respond dynamically to fluctuations in demand.
What does automated industrial production mean?
Automated industrial production involves the integration of technologies to improve efficiency and precision in production engineering. While production automation specifically targets manufacturing processes, industrial automation covers a broader spectrum that also includes other industrial areas such as energy and process engineering. This distinction is reflected in the different technical disciplines that play a central role in industry.
In process engineering the focus is on the development and optimization of processes in which raw materials are converted into products using physical, chemical or biological processes, such as in the production of chemicals, food or medicines. By using the latest technologies in process engineering, GREIF-VELOX is able to develop high-precision filling processes in which each batch is precisely adjusted to the desired volume and weight. This not only ensures consistently high product quality, but also minimizes deviations and losses, which is particularly important in the chemical and food industries.
The manufacturing technology focuses on the production of individual parts and assemblies using mechanical processing methods such as milling, turning, drilling or casting. GREIF-VELOX uses advanced automation solutions to make the entire packaging process efficient and flexible. Robots and automated systems take on tasks such as handling materials, closing packaging and final product inspection. This is a clear advantage for companies that rely on high throughputs and short production cycles.
In energy engineering, which deals with the generation, conversion and distribution of energy, automation is crucial for controlling power plants, optimizing networks and ensuring a stable energy supply. GREIF-VELOX integrates automation to optimize the energy consumption of its plants. Intelligent control systems monitor energy use in real time and adapt it to current production requirements. This reduces energy consumption and lowers operating costs.
Automation technology using the example of the fully automatic filling system A-DOS-P1
The A-DOS-P1 fully automatic filling system from GREIF-VELOX mentioned at the beginning combines innovative technologies such as automated bunghole detection, which ensures precise localisation and processing of openings on containers, and a state-of-the-art capping mechanism, which ensures fast and safe completion of the filling process.
In addition, the A-DOS-P1 has integrated weighing technology that measures and adjusts the exact weight of each filled batch in real time. This prevents overfilling or underfilling and guarantees consistent quality - a decisive advantage, especially in the chemical and food industries, where accuracy and efficiency must go hand in hand.
The system is also equipped with intelligent control systems that record, analyse and visualise production data in real time. This allows production parameters to be flexibly adjusted and optimised, resulting in a significant reduction in downtimes and more efficient use of resources.
Which processes can be automated in industrial production
In industrial production, a variety of processes can be automated to increase efficiency, precision and consistency.
Here are some of the key processes that are typically automated:
- Material transport and handling
Automated conveyor systems, automated storage and picking systems - Manufacturing and machining
CNC machines, industrial robots, 3D printing/additive manufacturing - Assembly
Robot-based assembly, automated screw and fastening systems - Quality control
Visual inspection systems, automated measuring and testing systems - Packaging and labeling
Automated packaging machines, labeling machines - Logistics and shipping
Automated transport systems, automated Sorting systems - Process monitoring and control
SCADA systems, process automation - Energy and resource management
Automated energy management systems, resource management systems - Maintenance and repair
Predictive maintenance - Data management and analysis
Big data and AI systems
How can these different processes be structured and integrated into industrial production to achieve end-to-end automation? The answer is provided by the automation pyramid. It represents a clear hierarchy of automation levels and serves as a guide for implementing and optimizing automation solutions. The automation pyramid shows how different processes in industrial production are linked and how information flows from one level to the next.
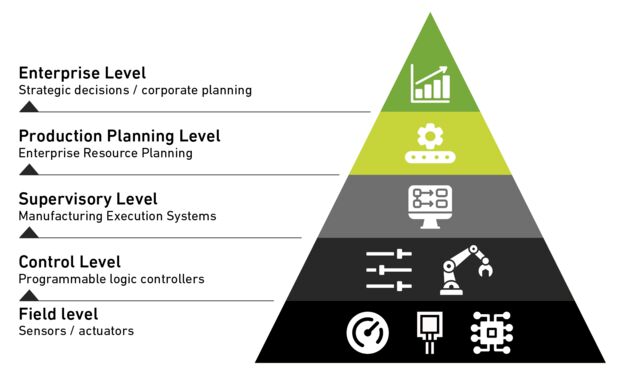
After the automation pyramid provides a systematic structure for the processes, automation technology implements these with technologies such as programmable logic controllers (PLCs), industrial robots and computer-aided machining (CNC). Automation technology standardizes and consolidates repeatable processes, which leads to higher production efficiency and consistent product quality. Automation technology also enables real-time monitoring and control of production processes and supports continuous process optimization through the integration of data management and analysis systems.
What does the automation pyramid mean in industrial processes?
The structure of the automation pyramid shows how data and information flow between the levels in order to make automation in industrial production holistic.
The levels of the automation pyramid in industrial production are:
The field level is the lowest level on which sensors, actuators and other field devices are located. These devices collect data and carry out physical actions. An automatable process in industrial production is the real-time monitoring and control of machines and production processes.
At the Control Level there are programmable logic controllers (PLCs) and other control systems that process the data from the field level and send corresponding control commands to the machines and systems. Automatable processes in industrial production are the automated control of production processes, machine control and control technology.
The Supervisory Level includes SCADA systems (Supervisory Control and Data Acquisition) and Manufacturing Execution Systems (MES), which monitor the processes, collect and analyze data, and provide an interface for the operators. In industrial production, the monitoring and optimization of production processes, process visualization and quality control can be efficiently supported and improved by automation technologies.
At the production planning level, systems such as enterprise resource planning (ERP) are used, which link production processes with other business processes, such as materials management, human resources management and logistics. In industrial production, production planning, materials management, resource management and supply chain optimization are processes that can be automated.
The top level is the management level (enterprise level). It includes strategic decisions and the entire company planning. Here, data from the lower levels is aggregated in order to make long-term decisions and control the company strategy. Processes such as business process management, strategic planning, cost optimization and company analysis can be supported and made more efficient by automation tools, whereby these tools are primarily used for data analysis and the automation of repetitive tasks.
What is automation technology?
Automation engineering is concerned with the development, application and integration of technologies for controlling, regulating and monitoring industrial processes in order to maximize efficiency, accuracy and flexibility in production, for example by improving Overall Equipment Effectiveness (OEE). Programmable logic controllers (PLCs), industrial robots, computer-aided machines (CNC) and sensors are used to optimize processes and reduce the need for human intervention. The use of these technologies increases operational reliability and ensures consistent production quality.
According to Mikell P. Groover's work "Automation, Production Systems, and Computer-Integrated Manufacturing" (2015), automation technologies are critical to creating modern, networked manufacturing environments. Groover emphasizes that these systems not only form the basis for today's industrial applications, but also represent central building blocks of Industry 4.0 by driving networking and real-time control in manufacturing.
What role does production automation play in the context of lean production?
Production automation plays a crucial role in the context of lean production. The study "Industry 4.0 Impacts on Lean Production Systems" by Tobias Wagner, Christoph Herrmann and Sebastian Thiede (2017) shows that the automation of processes within the framework of Industry 4.0 can significantly support the implementation of lean principles and increase their effectiveness.
Here are the seven most important goals of lean production that can be supported by production automation:
- Waste reduction (Muda)
Through precise control and optimization of processes, overproduction, rejects, unnecessary movements and waiting times can be minimized. - Continuous improvement (Kaizen)
Automated systems can be continuously monitored and analyzed, collecting process data in real time. This data serves as the basis for continuous improvement measures that can be implemented immediately. - Quality improvement
Automated quality control systems, such as visual inspection or automated measuring systems, help to detect and correct product defects at an early stage. This leads to consistently high product quality and reduces rework and waste. - Flexibility and responsiveness
By automating production processes, companies can respond more quickly to changes in demand, adjust production plans and efficiently manufacture different product variants. - Efficient use of resources
Automation enables more efficient use of resources through more precise control of material and energy use. - Just-in-time production
Automated logistics and production systems enable precisely coordinated production in which materials are available exactly when they are needed. Inventory levels are reduced and waste of resources is avoided. - Employee relief and engagement
Employees are relieved by automation taking over repetitive and physically demanding tasks.
What is Industry 4.0?
Industry 4.0 refers to the comprehensive networking of machines, data and people in production through the use of digital technologies aimed at enabling intelligent, autonomous and optimized production processes. According to the study "Smart Manufacturing: Past Research, Present Findings, and Future Directions" by Kusiak (2018), automation plays a central role here, as it includes the integration of networked, intelligent systems that allow production processes to be monitored, controlled and continuously optimized in real time. This is not just about the pure automation of machines, but about the creation of a "smart factory" in which machines, products and people communicate with each other through the Internet of Things (IoT). This networking makes it possible to collect and analyze production data in order to make processes more efficient and conserve resources.
According to the study "The Impact of Industry 4.0 on the Lean Production System" by Kolberg & Zühlke (2015), the connection with the principles of lean production is a central aspect of automation in Industry 4.0. Lean production aims to minimize waste and make value chains as lean and efficient as possible. Automation in an Industry 4.0 environment reinforces lean principles: processes are automated and optimized in real time, which can reduce waste, shorten production times and improve product quality.
In our article "Industry 4.0: Importance, challenges and benefits" we explain in detail the significance of Industry 4.0 for production companies.