Der Kunde

Die Omnisal GmbH produziert hochwertige Phosphate und Phosphatmischungen, die in über 85 Ländern von Unternehmen der Lebensmittelindustrie eingesetzt werden. Besonders in den Bereichen Fleisch, Meeresfrüchte, Käse- und Molkereiprodukte, Backwaren und Wein finden ihre Produkte Anwendung. Omnisal produziert und verarbeitet die Erzeugnisse am Standort Lutherstadt Wittenberg in Sachsen-Anhalt und gehört zusammen mit der Fosfa a.s. zur FB HOLDING Gruppe – dem größten Verarbeiter von gelbem Phosphor in Europa.
Die Ausgangssituation
Angesichts langfristiger Wachstumsperspektiven im Weltmarkt für Phosphor und Derivate entsprach die bisher eingesetzte Absackanlage nicht mehr den steigenden Anforderungen von Omnisal an Effizienz und Sauberkeit. Die veraltete Anlage konnte den wachsenden Produktionsvolumen und den hohen Hygieneansprüchen nicht mehr gerecht werden.
Die Anforderung
Omnisal wollte die Zuverlässigkeit, Produktivität, Hygiene und Absackleistung der Produktion deutlich steigern. Die Anforderungen umfassten:
- Eine vollautomatische Anlage zur sicheren und sauberen Absackung der unterschiedlichen Phosphatmischungen
- Integration einer bestehenden Abfüllanlage, die bereits 240 Säcke pro Stunde abfüllte
- Kurze Stillstandzeiten und Reinigungsintervalle bei Produktwechseln, um den Produktionsfluss nicht zu unterbrechen
Die Lösung
Omnisal entschied sich für eine Full-Line-Lösung – eine flexible Absackkomplettanlage inklusive modernster Robotik und Fördertechnik, die den wechselnden Phosphatrezepte vollautomatisch absackt. Die Lösung umfasst alle notwendigen Komponenten, um das Schüttgut hygienisch und effizient in Gebinde abzufüllen, zu etikettieren und palettiert versandfertig zu stapeln. Wesentliche Elemente der Lösung:
- „Hygienic Design“: Sämtliche Oberflächen, die mit dem Produkt in Berührung kommen, bestehen aus Edelstahl und erfüllen höchste Anforderungen der Lebensmittelverarbeitung.
- Perfekte Abstimmung: Alle essenziellen Komponenten – von den Greifwerkzeugen bis zur Roboterprogrammierung – stammen aus dem Hause Greif-Velox und gewährleisten höchste Güte und Prozesssicherheit.
- Hohe Absackleistung: Der BVPV 4.40 füllt Pulver, Granulate, Pellets oder Produktmischungen mit Korngrößen zwischen 50 µ und 12 mm in bis zu 240 Säcke oder 12 FIBC pro Stunde ab. Ein integriertes Magazin sorgt für die bedarfsgerechte Bevorratung und individuelle Etikettierung der Gebinde.
- Saubere, staubfreie Absackung: Das Aspiration Shield saugt während des Abfüllvorgangs austretende Stäube sofort auf, während die patentierte Ultraschallverschweißeinheit ValvoSeal für einen zuverlässigen und staubfreien Verschluss sorgt.
- Qualitätskontrolle: Das optische Messsystem ValvoDetect sortiert fehlerhafte bzw. fehlerhaft verschweißte Säcke vor der Palettierung aus, wodurch Verunreinigungen ganzer Paletten verhindert und Reklamationskosten reduziert werden.
- Automatische Palettierung: Mit dem Vier-Achs-Palettier-Roboter VeloPack werden die Säcke präzise und zeitsparend gestapelt, abschließend verschweißt, etikettiert und für den Versand vorbereitet.
- Reduzierte Stillstandzeiten: Dank spezieller Entleerungstechnik und effizienter Nassreinigungsfunktion konnten die Reinigungszeiten bei Produktwechseln um bis zu 80 Prozent minimiert werden.
Das Ergebnis: Kosteneinsparungen und hohe Prozesssicherheit bei Omnisal
Durch den Einsatz der neuen Full-Line-Absackanlage realisiert Omnisal signifikante Kosteneinsparungen und steigert gleichzeitig die Prozesssicherheit und Produktqualität. Die optimal aufeinander abgestimmten Anlagenkomponenten ermöglichen nicht nur eine zuverlässige Produktion, sondern bieten auch Potenzial für zukünftige Erweiterungen im Bereich Smart Industry.
Das durchgehende Hygienekonzept garantiert eine fehlerfreie und lebensmittelsichere Absackung, während alle relevanten Prozessdaten für datenbasierte Optimierungen erfasst und ausgewertet werden können.
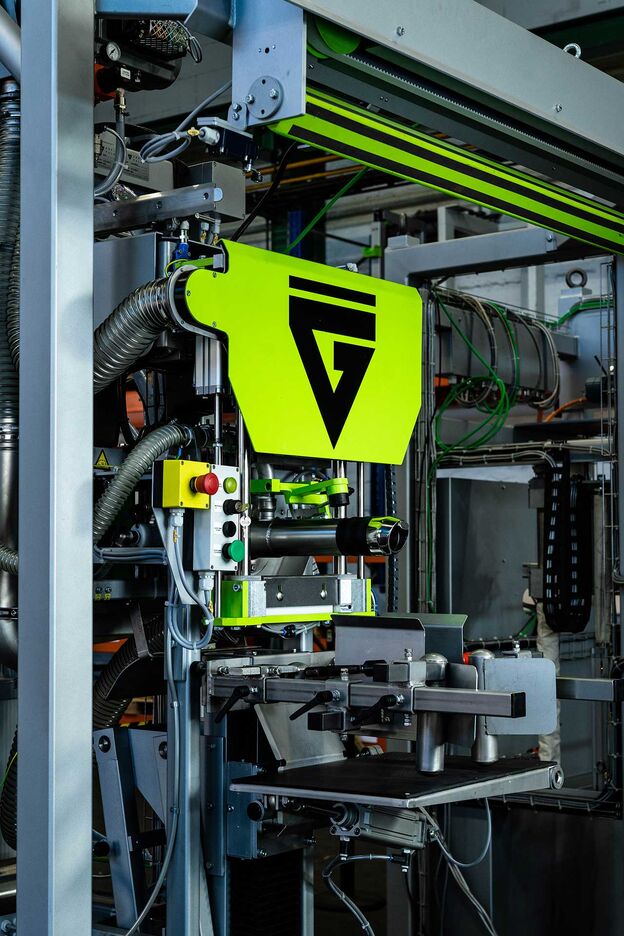
Schon mit der Abnahme bei Greif-Velox in Lübeck waren wir sehr zufrieden. Im Produktionsalltag kann die Anlage jetzt ihre Stärken ausspielen.
DALIBOR KUCHAR,
Omnisal
Signifikante Leistungssteigerung
Höchstmögliche Prozess- und Produktsicherheit
Einsparung von Personalkosten
Reduzierung der Reinigungs- und Reklamationskosten
Minimierung der Stillstandzeiten bei Produktwechseln