Der Kunde

Die GoodMillsGroup, Europas größtes Mühlenunternehmen, betreibt über ihre Tochtergesellschaft GoodMills Deutschland acht Standorte, an denen Qualitäts- und Spezialmehle, Hülsenfrüchte und Reis produziert werden. In der Hildebrandmühle in Mannheim fokussiert sich GoodMills Deutschland auf die Herstellung, das Absacken und die Verpackung verschiedener Hartweizenprodukte. Mit einer Jahreskapazität von mehr als 180.000 Tonnen zählt die Hildebrandmühle zu den größten Durum-Mühlen Deutschlands.
Die Ausgangssituation
Am Standort Mannheim plante GoodMills Deutschland, die bereits vielfältige Produktion um zwei zusätzliche Produktionslinien zu erweitern. Die bisherige Anlage konnte jedoch den aktuellen technologischen Entwicklungen nicht mehr standhalten und eine Erhöhung der Absackleistung war erforderlich. Aus diesem Grund entschied sich das Unternehmen für eine Investition in eine neue, flexiblere Anlage. Diese sollte nicht nur dem neuesten Stand der Technik entsprechen, sondern auch zukünftig erweiterbar und optimierbar sein, um kommenden Herausforderungen gerecht zu werden
Die Anforderung
Für die Expansion in Mannheim benötigte GoodMills Deutschland eine Anlage, die in der Lage ist, feine Mehle (mit einer Körnung unter 200 Mikrometer), feinkörnige Grieße (200 bis 800 Mikrometer) sowie Schrote (2 bis maximal 4 Millimeter) flexibel und präzise in Säcke zwischen fünf und 25 Kilogramm zu füllen
Die neue Abfüllanlage sollte die Möglichkeit bieten, Produktwechsel schnell und mit minimalem Reinigungsaufwand durchzuführen. Ein wesentliches Ziel war es, die Leistung im Vergleich zur alten Anlage zu verdoppeln und etwa 400 Säcke pro Stunde zu erreichen.
Zusätzlich sollte die Anlage bei Bedarf erweiterbar sein, um die Kapazität auf bis zu 600 Säcke pro Stunde zu steigern, ohne umfangreiche Umbaumaßnahmen durchführen zu müssen. Zudem war es erforderlich, dass die Anlagenkomponenten problemlos in bestehende Leit- und Steuerungssysteme integrierbar sind. Die Wahl fiel auf die GREIF-VELOX BVPV 4.40 Full-Line, die diese spezifischen Bedürfnisse erfüllt.
Die Lösung
GoodMills Deutschland entschied sich für den GREIF-VELOX Bruttopneumatikpacker BVPV 4.40, der durch innovative Technologie höchstmögliche Effizienz im Absackprozess von Grießen, Mehlen und Schroten gewährleistet. Diese Entscheidung führte zu einer erheblichen Optimierung der Produktionsprozesse.
Die Features
- Reibungslose Prozessabläufe und reduzierte Personalkosten:
Einsatz des GREIF-VELOX Valvomat, der den Leersack automatisch öffnet und korrekt auf den Füllstutzen positioniert - Reißfeste Verschweißung:
Die Ultraverschweißeinheit ValvoSeal mit patentierter Waffeltechnik sorgt für eine sichere Verschließung der Säcke nach dem Befüllen - Geringere Reklamationskosten:
Der platzsparende Kombi-Checker kombiniert einen Metall-Detektor mit einer integrierten Kontrollwaage, die mit einer Detektionsgenauigkeit von unter zwei Millimetern arbeitet - Automatische, präzise und zeitsparende Palettierung:
durch den Vier-Achs-Palettier-Roboter VeloPack - Automatischer Transport:
Die gefüllten Säcke werden über Rollenbahnen zu einem Wickler für die Ladungssicherung geleitet - Schnelle und einfache Produktwechsel:
möglich durch mechanische Features wie die motorische Sackstuhl-Höhenverstellung - Stetige Prozessoptimierung:
durch den „Gläsernen Packer“, der Prozessdaten erfasst, auswertet und verwaltet, was die Abfüllung verschiedener Produkte erleichtert - Deutlich reduzierte Reinigungsaufwände und -zeiten:
dank des pneumatisch aufklappbaren Restentleerbodens und einer speziellen Restentleerbarkeitsfunktion
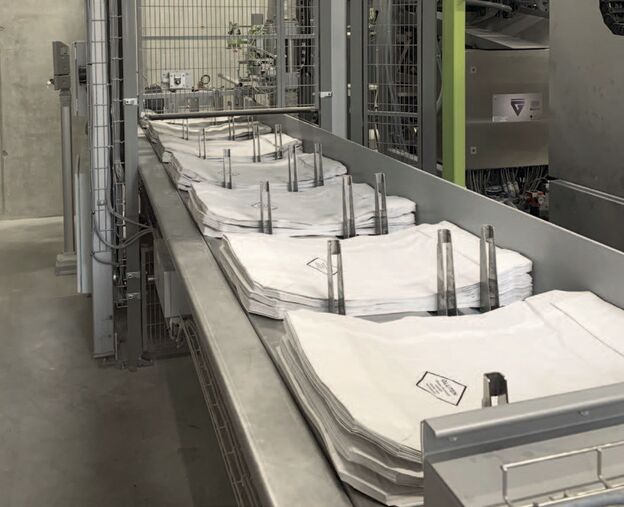
Das Ergebnis: Durchschlagender Erfolg bei GoodMills Deutschland
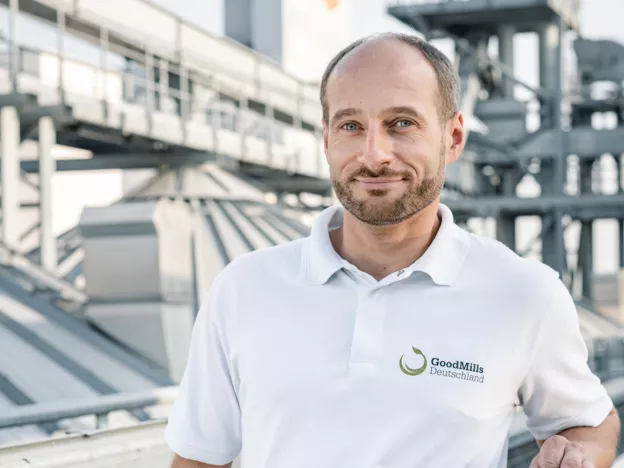
Mit der Implementierung der neuen Anlage von GREIF-VELOX konnte GoodMills Deutschland seine Produktionsleistung bereits verdoppeln. Darüber hinaus bietet die detaillierte Dokumentation der Prozessparameter die Möglichkeit, die Effizienz in der Zukunft weiter zu steigern. „Durch die Prozessdaten können wir die Abläufe noch besser aufeinander abstimmen“, erklärt Alexander Wieler, Werksleiter bei GoodMills. Er hebt hervor, dass die nahtlose Kommunikation zwischen den Maschinenkomponenten ein entscheidender Faktor für die Wahl von GREIF-VELOX war: „Die Programmierung aus einem Haus sorgt für klare Schnittstellen, im Gegensatz zu unseren Erfahrungen mit Mitbewerbern.“
Ein weiterer Vorteil der neuen Anlage ist der hohe Automatisierungsgrad, der es ermöglichte, eine Personalstelle einzusparen. Optimierungen wie der verbesserte Kesselauslauf reduzieren die Stillstandszeiten bei Produktwechseln erheblich, was die Produktivität weiter steigert. „Die Anlagen sind darauf ausgelegt, sehr gut leer zu fahren, was die Reinigungszeiten erheblich reduziert“, fügt Wieler hinzu. Produktwechsel werden durch die schnelle Auswahl eingespeicherter Abfüllparameter und Sackformate per Knopfdruck vereinfacht.
Zudem wurde durch den Einsatz eines platzsparenden und schnelleren Palettierroboters eine weitere Effizienzsteigerung erreicht. Wieler, der anfangs skeptisch war, ob der Roboter ein ebenso sauberes Palettenbild wie ein Lagenpalettierer liefern könnte, bestätigt: „Aber auch dieser arbeitet zur vollsten Zufriedenheit.“
GoodMills Deutschland profitiert zudem von dem zeitsparenden Remote-Service von GREIF-VELOX, der schnelle Unterstützung bei Inbetriebnahme, Konfiguration der Anlage und weiteren Fragen bietet. Dies stellt sicher, dass jederzeit ein Ansprechpartner zur Verfügung steht, um optimale Unterstützung zu gewährleisten.
Besonders positiv bei den Anlagen von GREIF-VELOX ist, dass es in allen Fragen immer einen Ansprechpartner gibt.
Alexander Wieler
Werksleiter bei GoodMills Deutschland
30 Prozent höhere Abfüllleistung
Höchstmögliche Mitarbeiter- und Produktsicherheit
Einsparung von Personalkosten
Reduzierung der Reklamationen
Kosteneinsparung durch Weiternutzung bestehender Produktionssysteme
Reduzierung der Stillstandzeiten durch zuverlässigen und schnellen Rundum-Service (mit Remote-Anbindung)