Interview with ICL Ladenburg: 100% clean bags and pallets
GREIF-VELOX: It's no longer a problem! The innovation for 100 percent clean bags and pallets. "...and we also have even more satisfied customers and a better brand reputation!"
In 2019, the engineers at GREIF-VELOX developed a technology that checks whether valve bags are correctly attached during bagging and can subsequently be sealed correctly. This check ensures that bags with a leaky seal are not palletized. The result is that no contamination occurs due to incorrectly positioned bags in the seal - a very important criterion with regard to hygiene requirements in the food industry and safety requirements in the chemical industry. This development was initiated by plant manager Thomas Jörder, an employee of our customer ICL at the Ladenburg site in Germany. Mr. Jörder was looking for a solution to reduce the complaint costs that his company had to bear as a result of leaking, poorly sealed bags.
Thomas Jörder talks about the background in an interview:
Mr. Jörder: How did you become aware of this problem?
Quite painful! Because every year we had complaint costs of at least 20,000 euros due to contaminated pallets. On top of that, there are also immaterial damages if customers are not satisfied with the delivery. The evaluation of a top-quality product must not fail because of a contaminated pallet.
What exactly was the cause of this contamination?
One reason, which is common across all industries and occurs from time to time: Some of the bags were not properly sealed. As a result, product escapes from this partially open valve. As a result, our customers then complain about entire pallets, which leads to high return transport costs.
Have you found the reason for the faulty welding?
Yes, it is due to fluctuations in bag quality or an incorrectly adjusted machine. As a result, it can happen that bags are not fitted 100 percent straight. If, for example, valve openings stick together, the bag is placed on the valve spout at an angle. Immediately after filling, the valve is also welded at an angle. Depending on the angle, it can happen that one side remains partially open and the product escapes at this point. During palletizing, this opening may then contaminate the entire pallet.
Is this a known problem?
Even a partially accepted one! The problem has existed across all industries for decades. Many companies are now even factoring in the cost of complaints. Thanks to the fact that GREIF-VELOX has now found a solution to this problem, we avoid around 20,000 euros in complaint costs every year and save ourselves a lot of time and effort in complaint management. An absolute added value for us: the bottom line is that we have even more satisfied customers and a better brand reputation!
Can you describe the solution in your own words?
Of course, because it is simple and logical: we now use a new optical measuring technology for our air packers, the GREIF-VELOX VALVO DETECT. The VALVO DETECT measures the angle at which the valve bags are fitted and if this angle is incorrect, meaning that the seal cannot be 100% correctly applied, the bag is not palletized and discharged. This means that we only have sealed bags on the pallet and no more contamination.
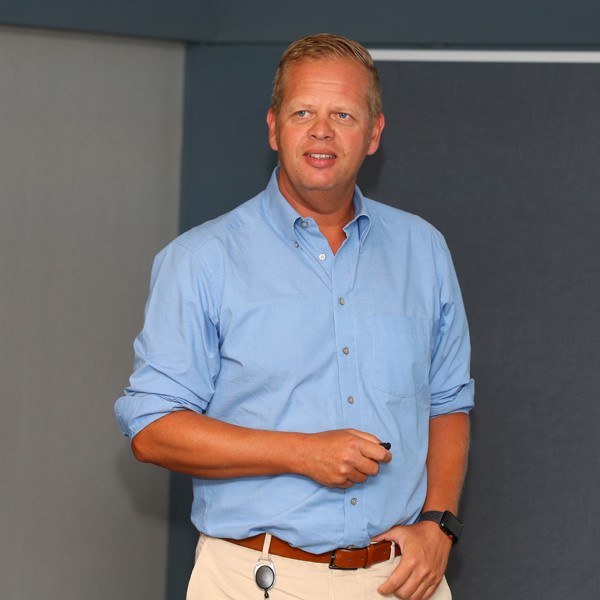
Thomas Jörder, ICL
About ICL
The ICL Group is a global manufacturer of mineral-based products used in agriculture, food and technical materials. As a successful chemical company, ICL generates sales of around USD 5.6 billion and employs around 11,000 people worldwide, including over 1,000 in Germany and Austria.
Around 450 employees work at the BK Giulini GmbH site in Ladenburg in the areas of development, production and sales of additives for: coatings and paints, the cosmetics and construction industries as well as for the food industry in the production of high-quality foodstuffs.