Finally bag flour and semolina efficiently and cleanly with BVPV 4.40
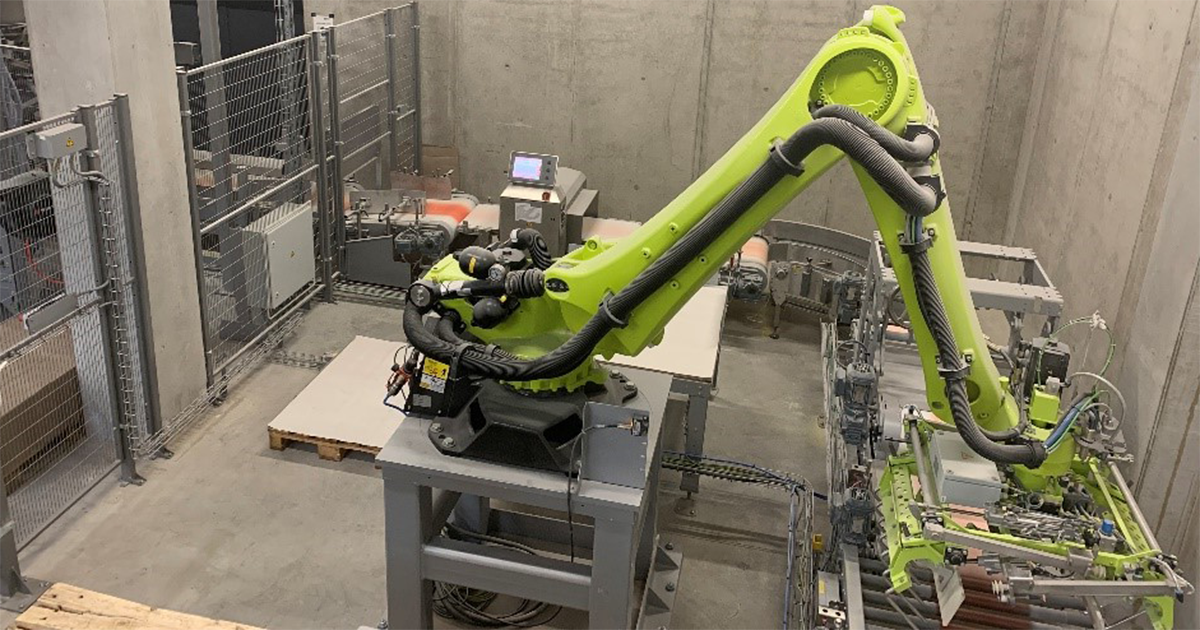
With the Greif-Velox BVPV 4.40 gross pneumatic packer and its innovative features, GoodMills Germany has doubled its bagging capacity at its Mannheim site
Short changeover and downtimes, maximum flexibility and lower investment: GoodMills Germany needed a system that can fill semolina and flour in different granulations into various bag sizes between 5 and 25 kilograms, depending on requirements, for its site in Mannheim. Machine manufacturer Greif-Velox supplied a compact solution in the form of the BVPV 4.40 gross pneumatic packer, which increased the bagging capacity by 100 percent compared to the old system. By evaluating the process data, efficiency can be increased even further in the future, as will be explained below.
With an annual capacity of more than 180,000 tons, the Hildebrandmühle in Mannheim is one of the largest durum wheat mills in Germany. Operator GoodMills Germany recently expanded the plant and added two further processing stages, couscous and bulgur, to its product range. This makes the company the only one north of the Alps to produce and package these products itself, alternating with others.
Flexible product changes with reduced changeover times
"We have a wide range of products that are filled with one machine - from semolina in various granulations, flours, couscous in various granulations to bulgur, which is more like coarse meal - everything from very coarse to very fine," says Alexander Wieler, plant manager in Mannheim. GoodMills Germany also had another requirement for the new machine: it had to be able to fill different products as well as different bag sizes between 5 and 25 kilograms with only short changeover and downtimes. "A major challenge," says Wieler.
Space-saving and compact
The packaging machine manufacturer Greif-Velox develops customized solutions for filling food and chemical products as well as full-line systems. With the BVPV 4.40 gross pneumatic packer and additional features, it has been able to create a system that precisely meets customer requirements. With the BVPV 4.40, 4 to 40 kilogram bags can be bagged with more than calibrated accuracy, depending on requirements. Depending on requirements, the integrated Flexchair can be adjusted to the desired bag size; the product flow is also controlled accordingly by a weighing system. This not only reduces product loss due to inaccurate filling, but also allows one machine to be used for different products and bag sizes in a space-saving manner and with a lower investment. "Together with the palletizing robots, Greif-Velox was able to create the most compact system," says plant manager Wieler. At the same time, it saves time: tedious, time-consuming adjustment is not necessary for bag format changes, but can be set at the touch of a button after the correct process parameters have been entered once. The same applies to product changeovers. Here too, saved, type-related machine parameters can be restored without any problems.
Residual emptying: Fast and hygienic product changeover without contamination
The quick and hygienic product changeover is made possible by the residual emptying process with special kettle outlet. Thanks to an innovative air rinsing system and a conveyor belt for the removal of product residues, significantly less residual product remains in the vat after the filling process than is usual in the industry, which results in annual savings in the five-digit euro range, depending on the bagging quantity. The system is also equipped with a pneumatically hinged residue discharge floor. "The systems are designed to empty very well," says Wieler. "This reduces cleaning times considerably."
Cleaning costs are reduced not only in the boiler, but also outside the plant, thus increasing employee safety: Clean filling with special return air nozzles with inflatable sleeves and return air ducting greatly reduces dust formation, especially with fine-grained products. "With the conventional machines, there was always a relatively high amount of dust escaping from the valves and a corresponding amount of cleaning work," says Alexander Wieler. "Now we only have very little contamination during normal operation."
Reduction of complaint expenses
To reduce complaint costs and ensure high product quality, the machine at the GoodMills Germany plant is also equipped with a space-saving combi-checker, which has a metal detector with a detection accuracy of less than two millimetres and also monitors the weight. In this way, any impurities can be detected and removed in good time before the products reach the end customer and potentially cause expensive and reputation-damaging recalls. Complaints are also reduced thanks to a particularly tear-resistant seal: The BVPV 4.40 features the ValvoSeal ultrasonic sealing unit, which seals valve bags securely and cleanly with a kind of waffle pattern. This ensures absolute tightness and, according to a study by the TH Lübeck, up to 60 percent higher tear resistance compared to conventional methods. This prevents product leakage and contamination of entire pallets.
Increased performance through evaluation of process data
With the BVPV 4.40, GoodMills Germany can now fill up to 400 bags per hour at the Mannheim site and achieve a maximum output of 600 bags per hour with an expansion variant. This means that the output has already doubled compared to the old system. But there is still room for further increases in efficiency. This is because the new system automatically collects process data and analyzes and evaluates it in the context of the overall system. In the long term, for example, downtimes due to incorrectly timed sub-processes can be avoided, "efficiency guzzlers" can be identified and storage capacities can be saved.
"We are still in the learning phase," says plant manager Alexander Wieler at the Mannheim site, where the system was put into operation around two months ago. "By evaluating the data, we will be able to further optimize the processes in the future."