The Five Most Important Developments in the Bagging of Carbon Black
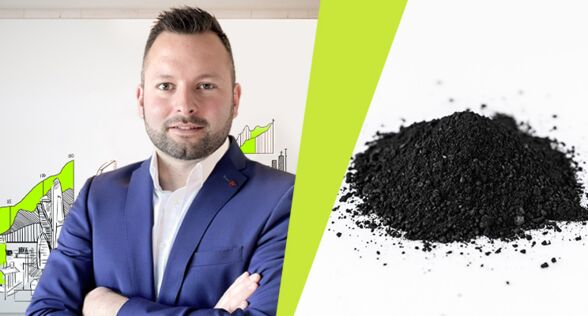
Blog article by Philipp Gschwindt, Area Manager and Key Account for Eastern Europe and Asia Pacific
Say goodbye to dirty business and hello to clean palletizing with the Greif-Velox vacuum technology VeloVac.
Imagine dust-free and highly compressed carbon black bagging with twice the usual number of bags neatly stacked on each pallet. This reduces your storage and logistics costs by up to 75%.
Greif-Velox VeloVac and its various features solve a long-standing problem in the industry. Why? Because our dust-free vacuum technology addresses these five crucial issues with bagging carbon black:
- Cleanliness and efficiency
- Lower costs for logistics, cleaning and material (e.g. reduction in bag consumption/wear)
- More flexibility
- Process reliability and safety
- Filling in FIBCs (big bags)
A dirty business: the conventional bagging process
The conventional bagging process of carbon black makes the production floor dusty, dirty, and overall very “black.” I frequently travel around the world to visiting leading manufacturers of carbon black and acetylene black. They all have the same problem: heavy contamination of the plant environment bringing along with it high cleaning costs, high logistics and complaint costs due to contaminated bags and increased risk for employees’ inhaling airborne dust. Ultra-light powders such as carbon black or its subform acetylene black (with particle sizes of less than 200 microns and a bulk density of less than 350 grams per liter), are the main culprit—when these powders are bagged, the entire plant environment is often contaminated, exposing employees to the hazardous dust. The bags and pallets themselves can also be contaminated, resulting in high cleaning and quality costs as well as damaging the brand’s reputation.
It doesn’t have to be this way.
Cleaner and more efficient with Greif-Velox VeloVac
Greif-Velox VeloVac technology eliminates the mess by enclosing the process in a vacuum chamber, making the bagging of ultra-light powder entirely dust-free. So both the operators and the surrounding area are clean and protected from emissions. The ultrasonic sealing unit Greif-Velox ValvoSeal ensures bags with a 70% higher seam stability compared to other systems on the market thanks to the patented “waffle welding” technology. Intelligent aspiration functions, such as the fully automatic nozzle, prevent contamination inside the valve and keep particles out of the active sealing surfaces.
Fewer boxes thanks to clean palletizing
There is also another outstanding benefit for the subsequent palletizing. Unlike conventional methods that involve dirty and bulky bags (filled with a lot of air) which are difficult to stack, the result with the Greif-Velox VeloVac is very different. Operators can safely stack far more bags on each pallet: twice as many layers, to be exact. Thanks to the dust-free vacuum process, the bags are highly compacted and clean, saving up to 75% on storage and logistics costs. Due to their brick-like, stable positioning, transport is safer and cheaper. A stable pallet also creates advertising space for your brand, increasing brand recognition.
Greif-Velox also offers various load securing systems in the end-of-line segment. iIn addition to a pallet wrapper, we offer shrink hood systems and stretch hood pullers that pull a fitted hood over the pallet to protect the load from damage during transport.
Safety is paramount
A number of features guarantee safety and cleanliness on various levels. Not only are employees protected from toxic emissions by bagging in a closed chamber, but the fully automatic version also requires no operator intervention, significantly increasing the safety of the employees and the process. In addition to extremely reliable sealing with Greif-Velox ValvoSeal, a cutting device (Greif-Velox ValvoCare) also ensures cleanliness by removing any valve overhangs that may be contaminated with product residue before they have a chance to contaminate the pallet. Integrated quality control, such as the valve tightness check and valve position check (Greif-Velox ValvoDetect), ensures that only the bags that meet your quality standards are palletized.
Greif-Velox Equipment Effectiveness (GVEE)
The Greif-Velox dashboard tools evaluate sensor data, giving users a complete overview of the entire process. These data can then be used for predictive maintenance as well as proactive optimization of process parameters in order to increase the overall system effectiveness going forward (GVEE = Greif-Velox Equipment Effectiveness).
Filling larger containers with Greif-Velox VeloVac XL
With our innovative Greif-Velox VeloVac XL model, users can now also fill FIBCs (big bags) with the vacuum method and benefit from the same advantages as with the VeloVac system for smaller containers: efficiency, cleanliness, employee safety, reducted storage, logistics and quality costs. Thanks to Greif-Velox VeloVac XL’s vacuum process, the FIBC shape is optimal for transport and storage. And last but not least, the filled FIBC does not need to rest after filling.
Completely flexible: the system grows with your requirements
From engineering to fully automatic operation, Greif-Velox offers everything you need from a single source: a team of engineers, project managers and process engineers will support you throughout the entire project. Our team will also assist you during commissioning to ensure that all integrated system components work together perfectly. We offer our VeloVac and VeloVac XL systems in various configurations depending on your unique requirements: from a manual to a full-line concept, which also includes complete system monitoring with bag and pallet tracking. Our systems are modular so you can flexibly upgrade to a higher automation level when needed.
We’d love to help you improve your bagging process! Feel free to contact us anytime with questions.