Smarter Packaging Through Smarter Industry
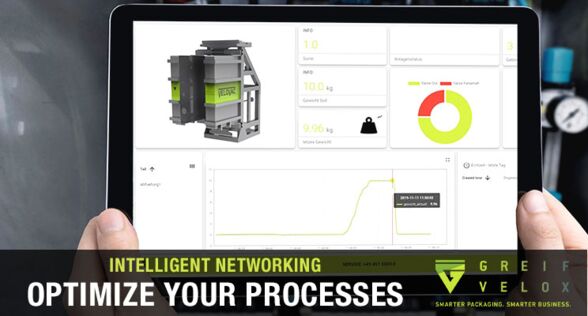
Decreasing storage capacities and the order-related individualization of products and product batches place great demands on both the production and packaging processes. The Greif-Velox machine factory therefore develops systems in the field of packaging systems that are individually tailored to customer requirements and that organize themselves and optimize processes thanks to intelligent networking. This brings clearly measurable advantages for planning, production, logistics and maintenance.
System messages, current weights, number of bags, current pressures, torques and more - all of these machine parameters of the filling process measured by sensors can be collected in a cloud thanks to a flexible data interface. This can be located locally in the Greif-Velox control system, the customer system or optionally also in cloud services. They are networked with the customer's process control system via application-specific IoT gateways.
Upgrade to Smart Industry possible for almost all systems
"Technical interfaces that we use, for example, are standard interfaces such as OPC UA or ProfiNet, with which you can directly access the data of the programmable logic controller," explains Benjamin John, Director of Engineering at Greif-Velox. "When it comes to the question of what kind of data should be transferred, we develop very individual solutions for our customers. We react very flexibly to the requirements and provide application advice - because usually much more is possible than the customers initially think." In this way, it is possible to upgrade any existing system to be smart industry-capable. This saves users costs on integration, as not every component has to be replaced.
Fundamental change in production and packaging processes
The use of sensor-monitored, cyber-physical systems fundamentally changes production and packaging processes. It is no longer the order planning that, for example, issues an order on paper to the system operator, who then sets the desired parameters on the machine. The process control system decides for itself which filling of which substance in which quantity would currently be most optimal and sends the information directly to the system via the inventory management system. This is possible through the central evaluation of the sensor data and the communication between the individual components, for example from pre-production, which report the status of the preliminary product to the system. In this completely digital process, downtimes due to sub-processes that are not correctly coordinated in time can be avoided. Storage capacity is also saved if the process is coordinated with the transport logistics so that the product is picked up directly after production.
Identification of efficiency guzzlers
The system control system also intervenes during the filling process in order to optimize the processes based on an intelligent data processing algorithm and information from neighboring processes. For example, the target and gross weight are constantly compared. If the gross weight deviates, the dosing unit reacts immediately and adjusts the filling quantity accordingly. Bags are thus filled optimally at all times under a wide variety of conditions.
"Based on the process data, we can automatically show how efficient the system is and where the efficiency guzzlers come from," says Benjamin John. In the future, this information can be displayed on a clear dashboard, which system operators can use to get an overview of the system's performance at any time and from any location via a VPN connection and also intervene in the production process. Customers benefit from higher output and increased efficiency.
Advantages for quality management
Smart networked systems also offer significant advantages for quality and complaint management. "If barcode labels are used to label products and corresponding scanners are used, specific containers can not only be identified, but specific data about them can also be stored," says Janis Feye, software developer at Greif-Velox. This makes it possible to record the torque when closing barrels in order to be able to prove that the closing process was correct later. If a complaint is made about a specific batch of a product, the production period and the cause of the problem can be identified more quickly and resolved sustainably by analyzing the data. This reduces complaint costs and increases the manufacturers' reputation with their customers with regard to the quality of the product.
Advances in predictive maintenance
In order to further increase machine performance and efficiency, the Greif-Velox team is also developing models to use the collected process data for predictive maintenance, i.e. proactive maintenance. "For this purpose, time, cycle and condition-based data are collected and evaluated," explains Benjamin John. In this way, the system can inform the user in good time before a possible failure if a system component needs to be replaced. Indicators of this can include the duration of use, but also deteriorated performance data. With timely maintenance, failures and downtimes in the production process can also be minimized. This means that the utilization of the machines is optimized, which leads to an overall increase in productivity.
With IoT developments in the field of packaging systems, Greif-Velox is pursuing continuous improvement in terms of flexibility, autonomy, performance, availability and transparency along the value chain.