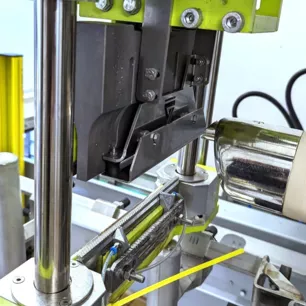
Product data ValvoDetect
Container | Valve bags made of paper, PE, PP |
---|---|
Industry | chemical, food |
Suitable systems | BVP and BVPV pneumatic packer systems |
Accessories & extensions | SmartValvoCut, ValvoSeal, ValvoMat |
ValvoDetect: The innovation for clean bags and pallets
The world's unique solution for clean bags and pallets
Additional cleaning and maintenance costs due to contaminated production lines
ValvoDetect minimizes product loss and reduces cleaning costs through precise error detection and elimination.
High complaint rates and customer dissatisfaction due to faulty valve bag welding
ValvoDetect detects and sorts out defective bags at an early stage, which ensures product quality and increases customer satisfaction.
Very expensive loss of time due to manual quality controls and post-processing
Automated testing processes of ValvoDetect increase the efficiency and throughput time of production.
Frequent production interruptions and downtime due to manual error corrections
ValvoDetect reduces downtime through automated error detection and correction, which increases production stability.
As part of a closed production system, our filling systems go far beyond the pure filling function: They form an integral part of an overall system that fits seamlessly into existing production lines and complements them.
Our full-line systems are able to serve complex requirements from container preparation and filling to post-processing and storage, which makes us a holistic system provider in production technology. The focus is on individual adaptation in order to ensure optimal integration into the respective operational processes.
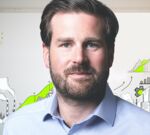
You save money with standard solutions.
You earn money with individual solutions.
Our philosophy at Greif-Velox is to offer individually tailored solutions instead of standard products.
Each filling system is tailored precisely to the needs and processes of our customers to enable rapid integration into existing product lines or the development of a completely coordinated full-line system.
We attach great importance to precision, safety and automation in order to increase our customers' production efficiency with maximum flexibility.
Find the right contact person
Direct contact to GREIF-VELOX or competent trading partner at your location:
You will find the right contact person for your request here.
Suitable GREIF-VELOX systems for filling valve bags
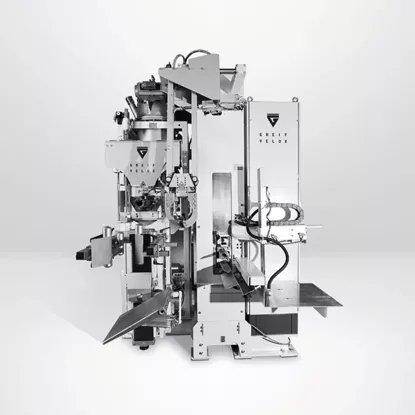
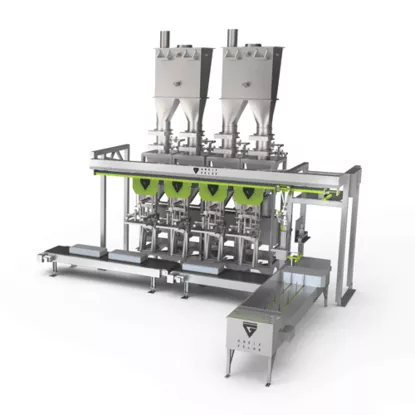
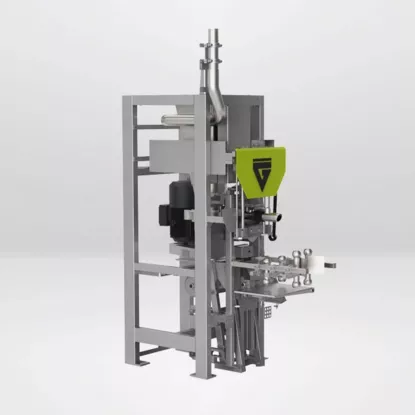